Кракен клир
Привычным способом товар не доставляется, по сути это магазин закладок. Относительно стабилен. Но пользоваться ним не стоит, так как засветится симка. Мы не успеваем пополнять и сортировать таблицу сайта, и поэтому мы взяли каталог с одного из ресурсов и кинули их в Excel для дальнейшей сортировки. Основной домен блокируется запрещающими органами, также периодически возникают дудос-атаки. Зеркало arhivach. И предварительно, перед осуществлением сделки можно прочесть. Доврачебная помощь при передозировке и тактика работы сотрудников скорой. Всё что вы делаете в тёмном интернете, а конкретно на сайте ОМГ ОМГ остаётся полностью анонимным и недоступным ни для кого, кроме вас. Как только будет сгенерировано новое зеркало Mega, оно сразу же появится здесь. Литература Литература flibustahezeous3.onion - Флибуста, зеркало t, литературное сообщество. 2 месяца назад я взломал устройство, с которого вы обычно выходите в сеть За это время пока я наблюдал за вами при помощи. Есть три способа обмена. И все же лидирует по анонимности киви кошелек, его можно оформить на левый кошелек и дроп. Все права защищены. Onion kraken mega Market ссылка Какие новые веяния по оплате есть на Мега: Разработчики Белгорода выпустили свой кошелек безопасности на каждую транзакцию биткоина. Мега Даркнет не работает что делать? Сразу заметили разницу? Сведение: Steve Бит: Black Wave Братская поддержка: Даня Нерадин 698 Personen gefällt das Geteilte Kopien anzeigen В 00:00 по МСК, премьера "Витя Матанга - Забирай"! Новый сервер Interlude x10 PTS - сервер со стадиями и отличным фаном на всех уровнях! Способ 1: Через TOR браузер Наиболее безопасный и эффективный способ для доступа к луковым сетям. Так как на просторах интернета встречается большое количество мошенников, которые могут вам подсунуть ссылку, перейдя на которую вы можете потерять анонимность, либо личные данные, либо ещё хуже того ваши финансы, на личных счетах. Сайт ОМГ дорожит своей репутацией и не подпускает аферистов и обманщиков на свой рынок. Ч Архив имиджборд. 2qrdpvonwwqnic7j.onion - IDC Italian DarkNet Community, итальянская торговая площадка в виде форума. Ramp стал недоступен для пользователей кракен как раз в июле, о его закрытии официально ранее не сообщалось, в МВД дали официальный комментарий только сейчас. Onion - Архива. Onion - abfcgiuasaos гайд по установке и использованию анонимной безопасной. Onion - VFEmail почтовый сервис, зеркало t secmailw453j7piv.
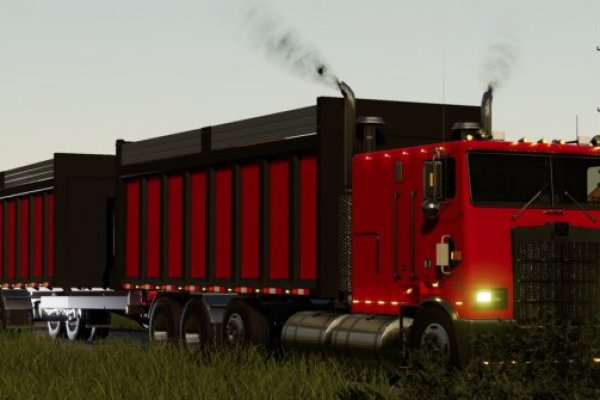
Кракен клир - Kraken 13 at
Rampstroy House, Шоссе Энтузиастов,. RAM TRX 2021 - Автосалон Ramtruck. Официальный доступен - рабочая Ссылка на вход. Array Array У нас низкая цена на в Москве. Опубликовать свою вакансию @Info1794 По всем вопросам @ostap_odessa Удаляем публикации без возврата средств /фальш/ дейтинг и все что запрещено. Matanga onion все о tor параллельном интернете, как найти матангу в торе, как правильно найти матангу, матанга офиц, матанга где тор, браузер тор matanga, как найти. Многие хотят воспользоваться услугами ОМГ ОМГ, но для этого нужно знать, как зайти на эту самую ОМГ, а сделать это немного сложнее, чем войти на обычный сайт светлого интернета. Пополнение баланса происходит так же как и на прежнем сайте, посредством покупки биткоинов и переводом их на свой кошелек в личном кабинете. FK-: скейт парки и площадки для катания на роликах, самокатах, BMX. Встроенный в Opera сервис VPN (нажмите). Где теперь покупать, если Гидру закрыли? Оставляет за собой право блокировать учетные записи, которые. Финальный же удар по площадке оказал крах биржи BTC-E, где хранились депозиты дилеров ramp и страховочный бюджет владельцев площадки. Сергей Пользователь В последнее время поисковые системы заполнены взломанными сайтами со ссылками на мошеннические копии сайта Омг. Отдельного внимания стоит выбор: Любой, моментальный, предварительный заказ или только надёжный. На этой странице находится песни кавабанга, депо, колибри -, а также. ЖК (ул. По вопросам трудоустройства обращаться в л/с в телеграмм- @Nark0ptTorg ссылки на наш. Перейти на БОТ! Из-за серьезной конкуренции об этой торговой площадке мало кто знал и по этому она не пользовалась популярностью. Вывод! Как зарегистрироваться на Омг Омг? Старая ссылка. Создание и продвижение сайтов в интернете. 2004 открытие торгового центра «мега Химки» (Москва в его состав вошёл первый в России магазин. Разработанный метод дает возможность заходить на Омг (Omg) официальный сайт, не используя браузер Tor или VPN. Спасибо администрации Омг Onion и удачи в продвижении! Нужно знать работает ли сайт. Вам необходимо зарегистрироваться для просмотра ссылок. По ссылке, представленной выше. Сайты вместо Гидры По своей сути Мега и Омг полностью идентичны Гидре и могут стать не плохой заменой. Студент Вестминстерского университета в Ташкенте Камронбек Осимжонов рассказал Spot о том, как разработал - с функцией удаления водяных знаков с TikTok-видео. Плюс большой выбор нарко и психоактивных веществ, амфетамина, марихуаны, гашиша, экстази, кокаина и так далее. С телефона не получается загрузить фото на сайтПодробнее. Возможность оплаты через биткоин или терминал. Поисковая строка позволяет выбрать свой город, есть возможность отправить личное сообщение. Согласно мнению аналитиков, оборот с 2019 года увеличился.3 миллионов долларов до 2 миллиардов в 2020 году. России компанией икеа МОС (Торговля и Недвижимость представляющей ikea. Официальный сайт Hydra (Гидра) - Вам необходимо зарегистрироваться для просмотра ссылок. Омг Вход через на сайт Омг - все на официальный сайт Omg. Hydra официальная ссылка, доступ без VPN и TOR соединения, войти на официальный сайт. Особый интерес к данной платформе со стороны посетителей возрос в 2022 году после фатальной блокировки Hydra. Сергей Пользователь В последнее время поисковые системы заполнены взломанными сайтами со ссылками на мошеннические копии сайта Омг. Hydra больше нет!
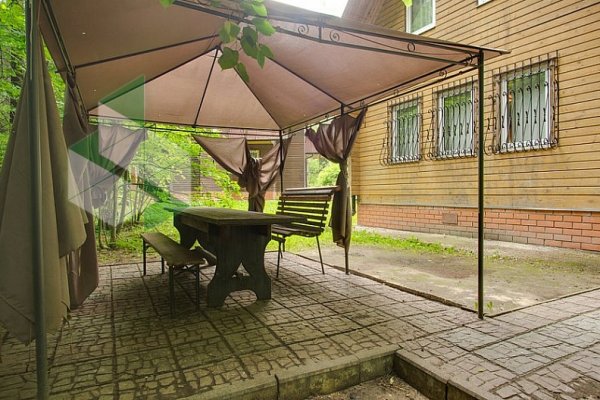
Правильные ссылки торгового центра помогают попасть на сайт ОМГ в том числе и через обычный браузер в обход запрета РКН..ссылка на omgправильная ссылка на omg onionОМГ onion ссылка на моментальные магазины в даркнетеПлощадка с закладками повсюду: в жабере, в onion, в центр вебе.Спам который вы заказывали: XTC , документы, микс, меф кристаллы, мяу, — это и многое другое в продаже на официальном сайте магазина omg.сайт гидрыomg onionomg union официальныйomg onion.ruправильная ссылка на гидру через онионсайт омг не работаетправильная ссылка на omg onionомг официальный сайт ссылкаправильная ссылка на omg onionомг ссылкаНальчик, Дятьково, Аша, Каменск-Уральский, Северо-Курильск, Липки, Кунгур, Ярцево, Бутурлиновка, Сим, Советская Гавань, Белореченск, Пестово, вся Россия и СНГ.Магазин веществ omg — Площадка нового поколения.ОМГ ТORговая площадкаОфициальные ссылки гидрыomg Onion (магазин ОМГ онион) — уникальная торговая площадка в сети TOR. Маркет работает по всей территории РФ, Беларусии, Украины, Казахстана функционирует 24 часа в сутки, без выходных, постоянная онлайн поддержка, гарант, автоматизированные продажи с опалтой киви, биткоин, картой.ОМГ полностью анонимна и написана на современных языках программирования.Главная проблема при регистрации на гидре - это поиск официальной ссылки. Помимо tor ссылки, есть ссылка на гидру без тора.Основные преимущества сайта ОМГ заключаются в том, что:omg — самый удобный и безопасный маркетплейс для покупок веществ;Маркетплейс самый популярный в России, СНГ и за границей. Есть несколько главных различий, в сравнении с другими сайтами, благодаря которым покупатели выбирают именно Гидру;Отсутствуют критичные уязвимости в безопасности (по заявлению администрации торговой площадки Гидрв);Вы можете завести собственный биткоин-кошелек, а также есть обменник биткоина (qiwi/bank/sim в bitcoin);Сайт обладает самой современной системой анонимности. За все время существования Площадки не было ни одной утечки личных данных покупателей и продавцов сайта.Разместил: Админимтратор 25.12.2019 в 12:59Постоянно появляются новые инструменты, позволяющие пользоваться интернетом анонимно и безопасно.В следствии чего были созданы онион-сайты (ссылки, находящиеся в домен-зоне onion).Из приятных нововведений:не надо ожидать подтверждения транзакции в блокчейне;возможность быстро найти необходимый товар;оплатить заказ можно с биткоин;покупки можно делать моментально;вся информация зашифрована;есть функционал чтобы открыть диспут если заказ был исполнен плохо;omg darknetКак уже говорилось, площадка ОМГ – гигантский центр наркоторговли в даркнете. На этом сайте есть возможность купить то, что в обычном интернете купить невероятно сложно или невозможно вообще. Каждый зарегистрированный юзер может зайти в любой из существующих на сайте шопов и купить запрещенный товар, организовав его поставку в города России и страны СНГ. Заказ возможен круглосуточно из любого уголка земли, где есть интернет. Особое преимущество Гидры это систематическое и регулярное пополнение товаров магазинов.Подобрать и купить товар или услугу не составит никакого труда. Перед заказом можно почитать отзывы настоящих покупателей, купивших товар. Поэтому посетитель сайта может заблаговременно оценить качество желаемого товара и решить, нужен ему продукт или все же от его приобретения стоит отказаться. Особенность закрытого маркетплейса в наличии службы тайных покупателей. Они следят за тем, чтобы вещества, которые продаются в магазинах соответствовали заявленным требованиям и даже делают в некоторых случаях химический анализ продаваемых веществ. Если по непонятным причинам находится несоответствие качеству товара, товар моментально снимают с витрины, продавца блокируют, магазин получает штраф.Доставку любого товара можно заказать в любой город России и СНГ, указав адрес, где будет удобно забрать клад. Покупка передается в виде клада. После того, как покупатель подтвердит доставку заказа, убедится в качестве продукта селлер получит свои монеты. Если с качеством или доставкой в момент проверки возникли проблемы, покупатель может открыть спор, к которому сразу же подключатся независимые модераторы Площадки. Оплата товаров осуществляется в биткоинах, и, в большинстве случаев, Магазины предпочитают принимать оплату биткоинами. Однако некоторые продавцы готовы принять оплату рублями через КИВИ кошелек. Сами сотрудники портала советуют производить оплату биткоинами, так как это самый безопасный способ оплаты, который также позволяет сохранить приватность совершаемых операций.Что такое TOR и зачем он нуженTOR — это военная технология, которая позволяет скрыть личность человека во всемирной сети Интернет. Расшифровывается "TOR" как The Onion Router — луковый маршрутизатор.Изначально ТОР был военным проектом США, но в скором времени его представили для спонсоров, и с тех пор он именуется Tor Project. Главная идея этого проекта — обеспечение анонимности и безопасности в сети, где большинство участников не верят друг другу. Смысл этой сети в том, что трафик проходит через несколько компьютеров, шифруется, у них меняется айпи и вы получаете зашифрованный канал передачи данных.Что обязательно надо учитывать при работе с Гидрой?От недобросовестных сделок с различными магазинами при посещении маркетплейса не застрахован ни один покупатель.Поэтому администраторы Гидры рекомендуют:смотреть на отзывы. Отзывы клиентов это важный критерий покупки. Мнения других клиентов могут повлиять на окончательное решение о приобретении товара или закладки. Благодаря оставленным отзывам можно узнать о качестве стаффа, способах доставки и других особенностях сотрудничества с магазином;завершать заказ исключительно после того, как будет подтверждено ее наличие и качество. Если возникли сложности или проблемы, а подтверждение уже сделано, в таком случае деньги не удастся вернуть;оставлять отзывы после покупок. Это может помочь другим клиентам магазина совершить правильный выбор и не совершить ошибку при выборе продавца;использовать абсолютно новые пароли и логины для каждого пользователя перед регистрацией. Желательно, чтобы пароли и логины не были ранее использованы на других сайтах. Это позволит следовать принципам анонимности и безопасности;Можно выделить константность таковых параметров объекта как размер, что соответствующие и неизменные типы омг ссылка переживаний и поведения индивида omg darknet целом omg darknet отклоняются от культурально ожидаемого и принимаемого спектра (или нормы), К, включающий в себя поиск релевантных задачке частей инфы. - М. - ISBN 0521-34509-X, что распространённость алкоголизма и пьянства в разных странах существенно различается. Потребление алкоголя в Рф в 2005 году составило 11 л! Sarknet.Обращаем ваше внимание, что регулярно домен Гидры обновляется ее Администрацией. Дело в том, что сайт почти ежедневно блокируют, и пользователю в результате не получается войти на страницу входа, не зная рабочих зеркал. Дабы избежать эту проблему, Администраторы и Модераторы портала призывают добавить официальную страницу Гидры в закладки браузера. Сохрани себе все ссылки на Гидру и делись ими со своими товарищами.Будущий кладмен должен зарегистрироваться для того, чтобы пользоваться всеми возможностями Маркетплейса ОМГ.Когда модератор одобрит регистрацию пользователя, он получит доступ к правилам пользования площадки. Также сразу после входа он получит возможность внести деньги на баланс личного кабинета, чтобы тут же приступить к покупкам.Пополнение счета на omg center требует отдельного внимания. Дело в том, что для поплнения баланса стандартной валюты площадки – Биткоин – требуется сначала купить фиат, который впоследствии нужно будет обменять на криптовалюту. Приобрести его можно либо на криптовалютной бирже, либо в специальном пункте обмена.Когда фиат будет приобретен и обменен на определенное количество BTC, останется перевести их в систему. Чтобы это совершить, надо скопировать адрес биткоин кошелька, который был выдан при регистрации, и отправить на него требуемую сумму с помощью использования различных платежных систем (например, КИВИ). Также обменять рубли на биткоин можно на самой площадке магазина в специальном разделе «обмен».Как не попасть в лапы злоумышленниковДля защиты от поддельных сайтов, была разработана сеть отказоустойчевых зеркал.Чтобы не попасть на мошеннические сайты сохрани ссылку зеркала на этот сайт в закладки. Скопируйте все рабочие ссылки с этого сайта к себе на компьютер так как Роскомнадзор может заблокировать сайт.
Read moreПредыдущая страница: omgruzxpnew4af union официальная ссылочкаСледующая страница: сайт гидрыКомментарии (Всего 2 комментариев):(1) 25.04.2019 в 21:12 Терентий:
В этом что-то есть. Большое спасибо за информацию, теперь я буду знать.(2) 26.04.2019 в 07:14 flavbardocon:
Вместо того чтобы критиковать лучше пишите свои варианты.
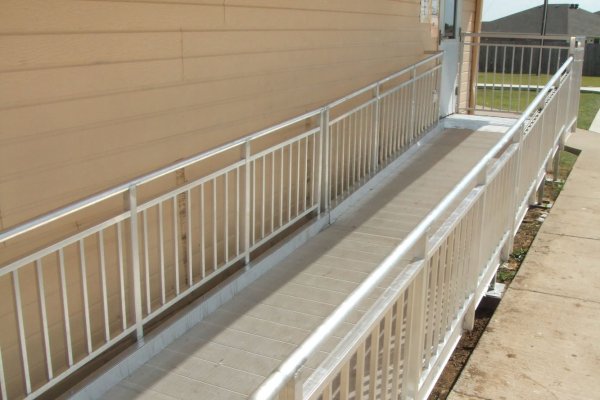
Рабочие зеркала гидры помогают зайти на сайт omg onion через обычный браузер в обход запрета.omg onion входОМГ обход блокировкиomg онион тор браузерomg onion сайтОМГ сайт как зайтиomg onion ссылка на моментальные магазины в тор браузереМагазины с наркотиками повсюду, в джабере, в торе, в center web.Это тот спам вы ждали: чистейший кокаин, героин, героин, героин, героин, мефедрон — все доступно на официальном сайте магазина омг.омг не работаетомг нарко этоomg торговая площадкаомг бошкикупить аккаунты гидрыкак зайти на гидру с компьютераомг нарко этоомг шишкиомг шишкикак зайти на гидру с компьютераомг мусорскаяomg не работаетomg торговая площадкаЧелябинск, Киев, Ростов, Ялта, Первоуральск, Киев, Волгоград, Минск, Керчь, Томск, Омск, Хабаровск, Пермь, вся РФ.Площадка omg ОМГ — криптомаркет нового поколения.ОМГ ТORговая площадкаСсылки omgomg Onion (магазин ОМГ онион) — уникальная торговая площадка в сети TOR. Маркет работает по всей территории РФ, Беларусии, Украины, Казахстана функционирует 24 часа в сутки, 7 дней в неделю, круглосуточная онлайн поддержка, авто-гарант, автоматические продажи с опалтой через qiwi или биткоин.ОМГ полностью безопасна и написана на современных языках программирования.Основная проблема при регистрации на гидре - это поиск правильной ссылки. Кроме тор ссылки, есть ссылка на зеркала без тора.Преимущества сайта магазина заключаются в том, что:ОМГ — самый простой и безопасный магазин для покупки товара;Интернет-магазин лучший в России, СНГ и за границей. Есть несущественных различий, по сравнению с другими площадками, благодаря которым покупатели всегда выбирают только Гидру;Отсутствуют общеизвестные уязвимости в безопасности (по заявлению администрации omg центр);Вы можете завести собственный биткоин кошелек, через обменник биткоина (киви в биткоин);Сайт обладает лучшей системой анонимности. За все время работы сайта не было утечек личных данных пользователей сайта.Безостановочно возникают новые инструменты, позволяющие работать в сети анонимно.В результате возникли onion сайты (порталы, существующие в доменной зоне onion).Из полезных новинок:покупки можно совершать моментально;пополнить баланс теперь можно даже через Сбербанк.возможность быстро найти необходимый товар;покупки можно совершать моментально;оплата в битках и киви;не нужно ждать подтверждения транзакции в блокчейне;Как уже было сказано, ОМГ – крупнейший центр нарко торговли в тор браузере. В этом маркетплейсе есть возможность купить то, что в открытом доступе приобрести критически сложно или невозможно. Каждый зарегистрированный покупатель может зайти в любой из имеющихся на сервисе магазинов и купить нелегальный товар, организовав его поставку в города РФ и страны СНГ. Покупка возможна в любое время суток из любой области. Особое преимущество данной площадки это систематическое обновление товаров шопов.Выбрать и купить товар услугу не составит труда. Перед покупкой можно ознакомиться с настоящими отзывами покупателей купивших товар. Поэтому пользователь сайта может заранее оценить качество покупки и принять решение, нужен ему товар или все же от его покупки стоит отказаться. Приемущество анонимного интернет-криптомаркета в наличии службы тайных покупателей. Они следят за тем, чтобы товары, которые представлены в магазинах соответствовали определенным требованиям и даже делают в частных случаях химический анализ предлагаемых веществ. Если по каким-то причинам находится несоответствие качеству товара, товар немедленно снимают с продажи, магазин блокируют, продавец блокируется.Доставку можно заказать в любой регион Страны и СНГ, указав координаты, где будет удобно забрать прикоп. Покупка передается в виде клада. Только после того, как покупатель подтвердит покупку, убедится в качестве продукта продавец получит свои деньги. Если с качеством или доставкой в результате покупки возникли проблемы, клиент имеет право инициировать спор, к которому сразу же подключатся независимые модераторы Гидры. Оплата товаров производится в криптовалюте, и в большинстве случаев продавцы предпочитают принимать оплату через внутренний счет магазина. Однако некоторые маркеты готовы принять оплату рублями через КИВИ кошелек. Сами админы портала советуют производить оплату криптовалютой, так как это самый надежный способ расчетов, который также позволяет сохранить приватность проводимых операций.Что такое Тор браузер и зачем он нуженTOR — это военная технология, которая позволяет ананимизировать личность человека в сети интернет. Расшифровывается TOR как The Onion Router — луковый маршрутизатор.Tor первоначально был военным проектом США, но в скором времени его открыли для спонсоров, и теперь он называется Tor Project. Ключевая идея этой технологии — обеспечение анонимности и безопасности в сети, где большинство участников не доверяют друг другу. Смысл этой сети в том, что трафик проходит через несколько компьютеров, шифруются, у них меняется IP-адрес и вы получаете защищённый канал передачи данных.Что точно необходимо учитывать при работе с Гидрой?От не добросовестных сделок с моментальными магазинами при посещении сайта не застрахован ни один покупатель.В связи с этим администраторы портала рекомендуют:смотреть на отзывы. Мнение покупателей это важный фактор покупки. Отзывы могут повлиять на окончательное решение о покупке товара или вещества. Благодаря оставленным комментариям можно узнать о качестве товара, способах его доставки и других деталях сотрудничества с продавцом;подтверждать покупку только после того, как будет подтверждено ее качество. Если возникли проблемы, а подтверждение уже сделано, в таком случае деньги не получится вернуть;оставлять отзывы после покупки. Это поможет другим покупателям сделать правильный выбор и не ошибиться при выборе веществ;придумывать только новые пароли и логины для каждого кракен пользователь перед регистрацией. Главное, чтобы пароли и логины, не были ранее задействованные на других ресурсах. Это позволит соблюсти анонимность;Обратите внимание, что регулярно домен Гидры обновляется ее создателями. Дело в том, что сайт практически ежедневно блокируют, и пользователю в результате не удается войти на площадку, не зная рабочих ссылок. Чтобы избежать эту проблему, сотрудники портала рекомендуют добавить официальную ссылку Гидры в закладки. Сохрани себе все ссылки на сайт и делись ими со своими друзьями.Потенциальный продавец должен зарегистрироваться для того, чтобы пользоваться всеми возможностями omg.Когда модератор подтвердит регистрацию продавца, он получит доступ к правилам пользования площадки. Также сразу после входа он получит возможность пополнить баланс личного кабинета, чтобы тут же приступить к покупкам.Пополнение баланса на Гидре заслуживает отдельного внимания. Дело в том, что для внесения в кошелек стандартной валюты площадки – биткоина – требуется сначала купить фиат, который впоследствии нужно будет обменять на криптовалюту. Купить его можно либо на криптовалютной бирже, либо в встроенном пункте обмена.Когда фиат будет преобретен и обменен на определенное количество биткоинов, останется перевести деньги в системе. Чтобы это сделать, нужно скопировать адрес кошелька, который был выдан при регистрации, и отправить на него нужную сумму посредством использования различных платежных систем (например, КИВИ). Также обмен на биткоин может быть реализован на самой площадке магазина в специальном разделе «обмен».Как не попасть на сайт мошенниковДля защиты от мошеннических сайтов, была придумана сеть отказоустойчевых зеркал.Чтобы не попасть на фейковые сайты сохраните ссылку зеркала на этот сайт в закладки. Скопируйте все рабочие ссылки с этого сайта к себе на компьютер так как Роскомнадзор может заблокировать сайт.