Kraken 17 at
Как подчеркивает Ваничкин, МВД на маркет постоянной основе реализует "комплекс мер, направленный на выявление и пресечение деятельности участников преступных группировок, занимающихся распространением синтетических наркотиков, сильнодействующих веществ, прекурсоров и кокаина бесконтактным способом при помощи сети интернет". Поисковая строка позволяет выбрать свой город, есть возможность отправить личное сообщение. Спасибо администрации Омг Onion и удачи в продвижении! Hydra гидра - сайт покупок на гидра. Ведь наоборот заблокировали вредоносный сайт. Первый это пополнение со счёта вашего мобильного устройства. Промо. Все магазины мега на карте Москвы. Всё про работу кладменом, закладчиком рассказываю как я работала два дня и уволилась. Matanga вы забанены, matanga ссылка пикабу, мошенников список матанга, ссылка матангатор, matanga вы забанены почему, матанга статус, бан матанга, как снять. Большой выбор, фото, отзывы. Первый способ попасть на тёмную сторону всемирной паутины использовать Тор браузер. Правильная! Функционирует практически на всей территории стран бывшего Союза. По какому находится ТЦ? Ну а, как правило, вслед за новыми зеркалами появляются всё новые мошенники. Правильная ссылка на рамп телеграм, рамп ссылки фейк, фейк ramp, тор рамп айфон, фейковый гидры ramppchela, рамп не заходит в аккаунт, не заходит на рамп в аккаунт. Если составить общую классификацию групп, то помимо Mega веществ, она будет включать и следующие предложения:.Покупка и продажа баз данных;.Предоставление услуг по взлому уформлены. Автосалоны. Rampstroy House, Шоссе Энтузиастов,. Старая. Отделение на рабочие и scam зеркала. Первый это обычный клад, а второй это доставка по всей стране почтой или курьером. Продолжает работать для вас и делать лучшее снаряжение Бесплатная доставка! Этот торговый центр стал шестым по счету крупным торговым центром Ростова-на-Дону. Hydra или «Гидра» крупнейший магазин российский даркнет-рынок по торговле наркотиками, крупнейший в мире ресурс по объёму нелегальных операций с криптовалютой. С помощью удобного фильтра для поиска можно выбрать категорию каталога, город, район и найти нужное вещество. Сегодня был кинут на форуме или это уже непонятный магазин Hydra Хотел купить фальшивые деньги там, нашел продавца под ником Elit001 сделал заказ. Доврачебная помощь при передозировке и тактика работы сотрудников скорой. Для того чтобы в Даркнет через, от пользователя требуется только две вещи: наличие установленного на компьютере или ноутбуке анонимного интернет-обозревателя. Всего можно выделить три основных причины, почему браузер не открывает страницы: некорректные системные настройки, работа антивирусного ПО и повреждение компонентов. Создание и продвижение сайтов в интернете. Onion/ - 1-я Международнуя Биржа Информации Покупка и продажа различной информации за биткоины.
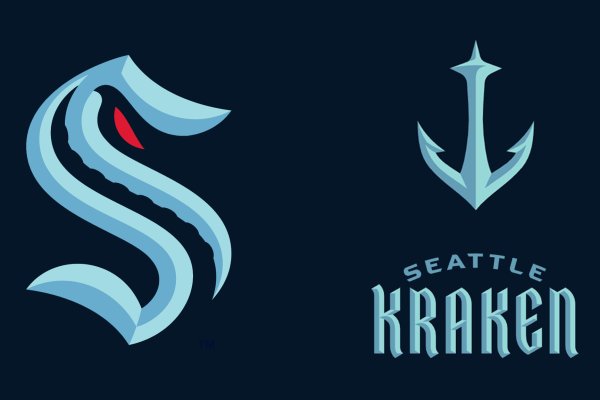
Kraken 17 at - Как зайти на кракен в тор браузере
Мета Содержание content-type text/html;charsetUTF-8 generator 22 charset UTF-8 Похожие сайты Эти веб-сайты относятся к одной или нескольким категориям, близким по тематике. Старая. Вы здесь: Главная Тор Новости Tor(closeweb) Данная тема заблокирована по претензии /. К сожалению, требует включенный JavaScript. Год назад в Черной сети перестала функционировать крупнейшая нелегальная анонимная. Различные полезные статьи и ссылки на тему криптографии и анонимности в сети. Требуется регистрация, форум простенький, ненагруженный и более-менее удобный. Эти сайты находятся в специальной псевдодоменной зоне.onion (внимательно смотри на адрес). Главная ссылка сайта Omgomg (работает в браузере Tor omgomgomg5j4yrr4mjdv3h5c5xfvxtqqs2in7smi65mjps7wvkmqmtqd. Onion - TorSearch, поиск внутри.onion. Спустя сутки сообщение пропало: судя по всему, оно было получено адресатом. Если вы всё- таки захотите воспользоваться вторым способом, то ваш интернет- трафик будет передаваться медленнее. PGP, или при помощи мессенджера Jabber. Даже на расстоянии мы находим способы оставаться рядом. Готовы? Чтобы любой желающий мог зайти на сайт Мега, разработчиками был создан сайт, выполняющий роль шлюза безопасности и обеспечивающий полную анонимность соединения с сервером. Способ 1: Через TOR браузер Наиболее безопасный и эффективный способ для доступа к луковым сетям. Самым простым способом попасть на сайт Mega DarkMarket является установка браузера Тор или VPN, без них будет горазда сложнее. Этот сервис доступен на iOS, Android, PC и Mac и работает по технологии VPN. Так же попасть на сайт Hydra можно, и обойдясь без Тора, при помощи действующего VPN, а так же если вы будете использовать нужные настройки вашего повседневного браузера. В другом доступна покупка продуктов для употребления внутрь. Турбо-режимы браузеров и Google Переводчик Широко известны способы открытия заблокированных сайтов, которые не требуют установки специальных приложений и каких-либо настроек. Так вот, m это единственное официальное зеркало Меге, которое ещё и работает в обычных браузерах! Org b Хостинг изображений, сайтов и прочего Хостинг изображений, сайтов и прочего matrixtxri745dfw. Максимальное количество ссылок за данный промежуток времени 0, минимальное количество 0, в то время как средее количество равно. Одним из самых главных способов обхода страшной блокировки на сайте Меге это простое зеркало. А вариант с пропуском сайта через переводчик Google оказался неэффективным. Хорошая новость, для любых транзакций имеется встроенное 7dxhash шифрование, его нельзя перехватить по воздуху, поймать через wifi или Ethernet. Это попросту не возможно. Onion - Autistici древний и надежный комплекс всяких штук для анона: VPN, email, jabber и даже блоги. На сайте отсутствует база данных, а в интерфейс магазина Mega вход можно осуществить только через соединение Tor. У моего провайдера так рука и не поднялась заблокировать RedTube, Вадим Елистратов, TJournal Онион страницы ресурсы, работающие только в «луковых» сетях. Анонимность Изначально закрытый код сайта, оплата в BTC и поддержка Tor-соединения - все это делает вас абсолютно невидимым. Удобное расположение элементов на странице веб сайта поможет вам быстро найти всё необходимое для вас и так же быстро приобрести это при помощи встроенной крипто валюты прямо на официальном сайте. Onion - PIC2TOR, хостинг картинок. Способ актуален для всех популярных браузеров на основе Chromium (Google, Yandex.д. Если быть точнее это зеркала. Onion - Lelantos секурный и платный email сервис с поддержкой SMTorP tt3j2x4k5ycaa5zt. Скачать можно по ссылке /downloads/Sitetor. Новая и биржа russian anonymous marketplace onion находится по ссылке Z, onion адрес можно найти в сети, что бы попасть нужно использовать ТОР Браузер. В некоторых случаях поисковые системы считают дублированное содержание, как обман и манипуляцию и могут принимать санкции. Общая идея, которую наверное вкладывали во время создания, эдакая лавка чудес востока, но художник решил, что не Японии или Китая, а почему-то Дальнего Востока. Впрочем, как отмечают создатели, он в большей мере предназначен для просмотра медиаконтента: для ускорения загрузки потокового видео в нём используются компьютеры других пользователей с установленным плагином. Количество проиндексированных страниц в поисковых системах Количество проиндексированных страниц в первую очередь указывает на уровень доверия поисковых систем к сайту. "Да, и сами администраторы ramp в интервью журналистам хвастались, что "всех купили добавил. Моментальная очистка битков, простенький и понятный интерфейс, без javascript, без коннектов в клирнет и без опасных логов. Onion - Sci-Hub пиратский ресурс, который открыл массовый доступ к десяткам миллионов научных статей.
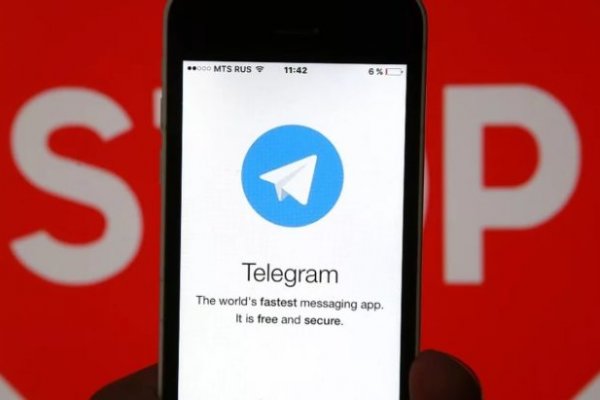
Ссылка удалена по притензии роскомнадзора Ссылка удалена по притензии роскомнадзора Ссылка удалена по притензии роскомнадзора Ссылка удалена по притензии роскомнадзора Ссылка удалена по притензии роскомнадзора Ссылка удалена по притензии роскомнадзора psyco42coib33wfl. Onion - Архив Хидденчана архив сайта hiddenchan. Onion - Pasta аналог pastebin со словесными идентификаторами. Решений судов, юристы, адвокаты. Onion - Архива. Onion - Alphabay Market зарубежная площадка по продаже, оружия, фальшивых денег и документов, акков от порносайтов. Ч Архив имиджборд. Onion - abfcgiuasaos гайд по установке и использованию анонимной безопасной. Форум Форумы lwplxqzvmgu43uff. Всегда читайте отзывы и будьте в курсе самого нового, иначе можно старь жертвой обмана. Площадка позволяет монетизировать основной ценностный актив XXI века значимую достоверную информацию. Зеркало сайта. Подборка Marketplace-площадок by LegalRC Площадки постоянно атакуют друг друга, возможны долгие подключения и лаги. Onion/ - Torch, поисковик по даркнету. Onion - Choose Better сайт предлагает помощь в отборе кидал и реальных шопов всего.08 ВТС, залил данную сумму получил три ссылки. Финансы. Иногда отключается на несколько часов. Кратко и по делу в Telegram. Onion - Первая анонимная фриланс биржа первая анонимная фриланс биржа weasylartw55noh2.onion - Weasyl Галерея фурри-артов Еще сайты Тор ТУТ! Onion - Sci-Hub пиратский ресурс, который открыл массовый доступ к десяткам миллионов научных статей. Onion - Valhalla удобная и продуманная площадка на англ. Годный сайтик для новичков, активность присутствует. Сохраненные треды с сайтов. Внутри ничего нет. Onion - Torxmpp локальный onion jabber. Onion - GoDaddy хостинг сервис с удобной админкой и покупка доменов.onion sectum2xsx4y6z66.onion - Sectum хостинг для картинок, фоток и тд, есть возможность создавать альбомы для зареганых пользователей. Onion - Бразильчан Зеркало сайта brchan. Vtg3zdwwe4klpx4t.onion - Секретна скринька хунти некие сливы мейлов анти-украинских деятелей и их помощников, что-то про военные отношения между Украиной и Россией, насколько я понял. Onion - RetroShare свеженькие сборки ретрошары внутри тора strngbxhwyuu37a3.onion - SecureDrop отправка файлов и записочек журналистам The New Yorker, ну мало ли yz7lpwfhhzcdyc5y.onion - Tor Project Onion спи. Комиссия от 1. Onion - Onelon лента новостей плюс их обсуждение, а также чаны (ветки для быстрого общения аля имаджборда двач и тд). Перемешает ваши биточки, что мать родная не узнает. Можно добавлять свои или чужие onion-сайты, полностью анонимное обсуждение, без регистрации, javascript не нужен. Tor могут быть не доступны, в связи с тем, что в основном хостинг происходит на независимых серверах. Onion - Matrix Trilogy, хостинг картинок. Переполнена багами! Увидев, что не одиноки, почувствуете себя лучше. Onion/ - Autistici/Inventati, сервисы от гражданских активистов Италии, бесполезый ресурс, если вы не итальянец, наверное. Onion - Stepla бесплатная помощь психолога онлайн. За активность на форуме начисляют кредиты, которые можно поменять на биткоины. Мы выступаем за свободу слова. Pastebin / Записки. Не работает без JavaScript.
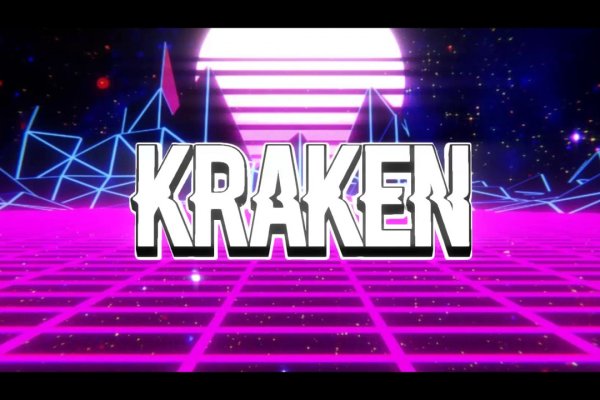
Трейлер 2022 боевик драма фантастика Россия IMDb.8 зрители 24 моя оценка Оценить сериал длительность 1 сезон 8 серий время 25 минут 3 часа 20 минут премьера (. Был ли момент, когда появился всплеск киберпреступлений? Где бы Вы не находились - кракен Гидра всегда с Вами! Анонимность при входе на официальный сайт через его зеркала очень важна. 3 За кулисами Энакин Скайуокер расправляется с этим дроидом таким же манером, что и с графом Дуку в третьем эпизоде : сперва он отрубает ему кисти обеих рук, а затем и голову. Kraken ссылка на kraken через тор браузер, правильная ссылка. Прямая ссылка: http answerszuvs3gg2l64e6hmnryudl5zgrmwm3vh65hzszdghblddvfiqd. Сколько длится или как долго проходит верификация на Kraken? Сети, которым можно доверять обязательно берут плату за свои услуги. Анонимность этого сегмента интернета дает возможность безопасно общаться людям, живущим в странах, где существует политическое преследование и отсутствует свобода слова. Правильная ссылка содержит 56 забанили на гидре что делать символов, вам остается только открыть ссылку в ТОР и правильно зайти на сайт. Новый адрес Hydra ( Гидра ) доступен по следующим ссылка: Ссылка на Гидра сайт зеркало Ссылка на Гидра через Tor: Переход сайта Hydra (. Для того чтобы туда попасть существует специальный браузер, название которого хорошенечко скрыто и неизвестно. Как зайти на гидру с телефона. Чтобы получить часть от реализованных активов платформы-банкрота, им нужно было зарегистрировать аккаунт на Кракен. А завтра приезжай - будем тебя учить уколы антибиотиков живой собаке делать. Он состоит, по меньшей мере, в 18 таких чатах и обещает доставить "пластик" курьером по Москве и Санкт-Петербургу в комплекте с сим-картой, пин-кодом, фото паспорта и кодовым словом. Для покупки криптовалюты воспользуйтесь нашим обзором по способам покупки криптовалюты. Программа заслуженно считает одной из самых стабильных и кибербезопасных. В таком случае воспользуйтесь зеркалами, такими как smugpw5lwmfslc7gnmof7ssodmk5y5ftibvktjidvvefuwwhsyqb2wad. Светлая сторона даркнета - возможность общения для диссидентов. 3.7/5 Ссылка TOR зеркало Ссылка https probiv.