Кракен наркокортель
Home Admin 2018-12-09T16:24:21+00:00Take control of your media assets100% free, open source software released under GPL 3.0Easy to use media web gallery you install on your web serverUnlimited albums, media files and usersQuickly build your gallery by synchronizing with кракен existing photos, videos, audio files, and documentsOrganize — tag, edit, rotate and moreUse any browser on any device — no client software or pluginsFirst class touch support.Creates web-friendly versions of your large files — even videosSecure gallery access — granular, per-album permissionsEasy installation on any IIS 7+ web server, including Windows hosting providersTake кракен control of your media assetsNo-fuss student galleriesShare photos and videos with friends and relativesMeet the TeamRoger Martin, Founder and Lead DeveloperI have been passionate about media management and online galleries since releasing the first version of Gallery Server 10 years даркнет ago. This is what I love.
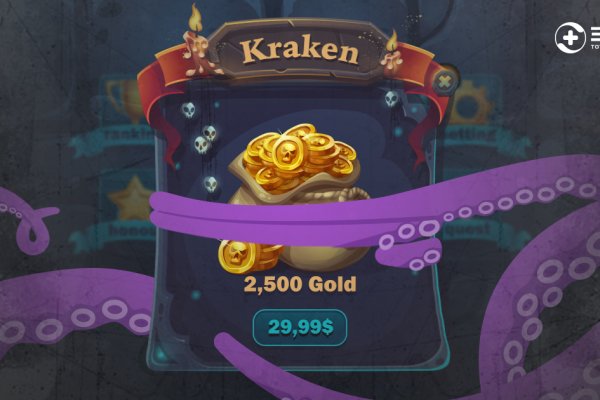
Кракен наркокортель - Кракен даркнет стор
е общение, обсуждение как, бизнеса, так и других андеграундных тем. Как использовать. Отключив серверы маркета, немецкие силовики также изъяли и крупную сумму в криптовалюте. Из-за этого в 2019 году на платформе было зарегистрировано.5 миллиона новых аккаунтов. Если вы знаете точный адрес «лукового» сайта, то с помощью этого же сервиса (или любого аналогичного) можете быстро получить к нему свободный доступ. Читайте также: Восстановить пароль виндовс 7 без установочного диска. Onion - 24xbtc обменка, большое количество направлений обмена электронных валют Jabber / xmpp Jabber / xmpp torxmppu5u7amsed. Рейтинг продавца а-ля Ebay. Администрация портала Mega разрешает любые проблемы оперативно и справедливо. Меня тут нейросеть по фоткам нарисовала. Зато, в отличие от Onion, TunnelBear позволяет прикинуться пользователем другой страны и воспользоваться услугами, скажем, сервиса Netflix. Источник Источник. Проект создан при поддержке форума RuTor. Низкие цены, удобный поиск, широкая география полетов по всему миру. Всё что нужно: деньги, любые документы или услуги по взлому аккаунтов вы можете приобрести, не выходя из вашего дома. Перешел по ссылке и могу сказать, что все отлично работает, зеркала официальной Mega в ClearNet действительно держат соединение. Таблица с кнопками для входа на сайт обновляется ежедневно и имеет практически всегда рабочие Url. Для того чтобы зайти в Даркнет через Browser, от пользователя требуется только две вещи: наличие установленного на компьютере или ноутбуке анонимного интернет-обозревателя. Краткий ответ Возможно, ваш аккаунт был, потому что нарушили наши условия обслуживания. Английский язык. Форумы. Например, такая интересная уловка, как замена ссылки. Ещё есть режим приватных чат-комнат, для входа надо переслать ссылку собеседникам. Перевалочная база предлагает продажу и доставку. В платных аках получше. Russian Anonymous Marketplace один из крупнейших русскоязычных теневых форумов и анонимная торговая. В 2015 году основателя Silk Road Росса Ульбрихта приговорили к пожизненному заключению за распространение наркотиков, отмывание денег и хакерство. Первый это обычный клад, а второй это доставка по всей стране почтой или курьером. Минфин США ввело против него санкции. Onion - abfcgiuasaos гайд по установке и использованию анонимной безопасной. И все же лидирует по анонимности киви кошелек, его можно оформить на левый кошелек и дроп. Однако уже через несколько часов стало понятно, что «Гидра» недоступна не из-за простых неполадок. Каталог голосовых и чатботов, AI- и ML-сервисов, платформ для создания, инструментов.возврата средств /фальш/ дейтинг и все что запрещено Законами Украины. В бесплатной версии приложения доступно всего 500 мегабайт трафика в месяц, а годовой безлимит обойдется в 979 рублей (и это только цена для устройств на iOS). Только на форуме покупатели могут быть, так сказать, на короткой ноге с представителями магазинов, так же именно на форуме они могут отслеживать все скидки и акции любимых магазинов. Playboyb2af45y45.onion - ничего общего с журнало м playboy journa. Просмотр.
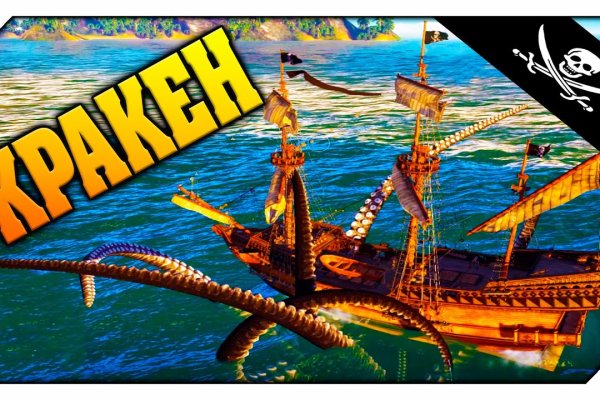
Стать нашими клиентами очень просто. За все время работы площадки не было ни одной утечки личных данных пользователей и продавцов сайта. Сервис от Rutor. I2P не может быть использована для доступа к сайтам. Основная проблема при регистрации на гидре - это поиск правильной ссылки. Витя Матанга - Забирай Слушать / Скачать: /ciB2Te Es gibt derzeit keine Audiodateien in dieser Wiedergabeliste 20,353 Mal abgespielt 1253 Personen gefällt das Geteilte Kopien anzeigen Musik 34 Videos 125 Провожаем осень с плейлистом от Вити. Аккаунты omg с балансом бесплатно. Комментарий пока не оценивали 0Ответить Добавить в закладки Ещё MrB4el в14:35Показать предыдущий комментарийОсновной рынок работы гидры - страны СНГ (где с ней безуспешно"боролись" несколько лет дальше сами делайте выводы, исходя изпоследнего месяца. Содержание Подробности Главное достоинство Tor Browser заключается в том, что он максимально сильно скрывает местоположение и прочие данные пользователя в ходе интернет-серфинга. Зеркало сайта. Безостановочно появляются новые инструменты, позволяющие действовать в сети анонимно. Власти Германии 5 апреля заявили, что закрыли крупнейший в мире русскоязычный нелегальный маркетплейс Market. Хороший и надежный сервис, получи свой. Если у вас возникли проблемы, пожалуйста, воспользуйтесь формой обратной связи. Host Как найти адрес крамп. Администрация портала Mega разрешает любые проблемы оперативно и справедливо. На Kraken торгуются фьючерсы на следующие криптовалюты: Bitcoin, Ethereum, Bitcoin Cash, Litecoin и Ripple. На смартфоне человека, обычно, хранится важная финансовая информация, которая естьнамерением преступников. Сведения об уплаченных организацией суммах налогов и сборов за 2021 год Страховые и другие взносы на обязательное пенсионное страхование, зачисляемые в Пенсионный фонд Российской Федерации 0 руб. 2048-битное SSL-шифрование скрывает банковскую информацию, пароли, письма и другие важные данные от посторонних. Telegram боты. Чтобы это сделать, нужно скопировать адрес кошелька, который был выдан при регистрации, и отправить на него нужную сумму посредством использования различных платежных систем (например, киви). Сытов Антон Викторович также руководит АО «ньюлевел». Особое преимущество этой площадки это частое обновление товаров шопов. Как мы знаем "рынок не терпит пустоты" и в теневом интернет пространстве стали набирать популярность два других аналогичных сайта, которые уже существовали до закрытия Hydra. Заказать, эстакаду с доставкой от производителя апшерон, в наличии. Отзыв не должен нести в себе расовую, национальную, половую или другие виды дискриминации, а также нарушать действующее законодательство. Сайт. Ему дают адрес и фотографию закладки, которую и предстоит отыскать. Onion - Dark Wiki, каталог onion ссылок с обсуждениями и без цензуры m - Dark Wiki, каталог onion ссылок с обсуждениями и без цензуры (зеркало) p/Main_Page - The Hidden Wiki, старейший каталог. Обязательный отзыв покупателя после совершения сделки. Onion недоступен. 2 дня. Onion - Alphabay Market зарубежная площадка по продаже, оружия, фальшивых денег и документов, акков от порносайтов. Она менее популярна и не может быть использована для доступа к обычным сайтам. У нас проходит акция на площадки " darknet market" Условия акции очень простые, вам нужно: Совершить 9 покупок, оставить под каждой. Когда фиат будет преобретен и обменен на определенное количество биткоинов, останется перевести деньги в системе. Но есть важное различие между тем, как они связываются между собой. Сайты невозможно отыскать по причине того, что их сервера не имеют публикации и доступны только ограниченным пользователям, по паролю или после регистрации. В случае компрометации пароля злоумышленник не сможет попасть в аккаунт, так как он будет защищен ещё и двухфакторной авторизацией. Например, сайт BBC недоступен в таких странах. Также обмен в bitcoin может быть реализован на самой площадке в специальном разделе «обмен».Как не потерять деньги на сайте мошенниковДля защиты от обманных сайтов, была придумана сеть отказоустойчевых зеркал. А ещё ссылка его можно купить за биткоины. Адрес 142324, Россия, Московская область, город Чехов, деревня Люторецкое, территория промзона Люторецкое, владение 6, строение 1, Телефон 8 (495) Проезд к складу По Симферопольскому шоссе в сторону. После того, как покупатель подтвердит покупку, удостоверится в качестве продукта продавец получает свои деньги. Читайте полную статью: Верификация на бирже что нужно знать о KYC и AML Трейдинг на бирже Kraken Для того, чтобы начать торговлю на Kraken, необходимо: Перейти на страницу торгов. Прямая ссылка: http answerszuvs3gg2l64e6hmnryudl5zgrmwm3vh65hzszdghblddvfiqd. Подобный контроль ограничивает как личную свободу, так и приватность деловых связей и контактов. TOR Для компьютера: Скачать TOR browser.
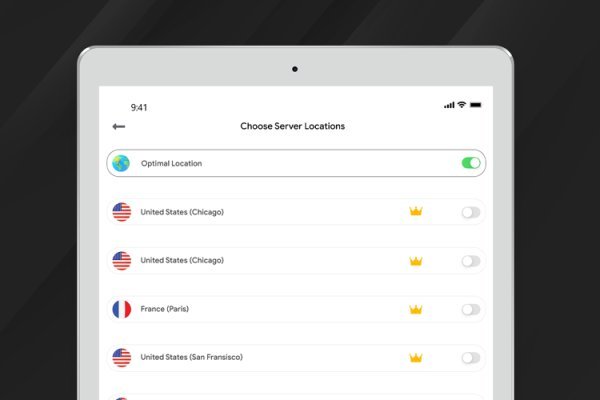
Сохраните где-нибудь у себя в заметках плейс данную ссылку, чтобы иметь быстрый доступ к ней и не потерять. Основные усилия направлены на пресечение каналов поставок наркотиков и ликвидацию организованных групп и преступных сообществ, занимающихся их сбытом». Kkkkkkkkkk63ava6.onion - Whonix,.onion-зеркало проекта Whonix. Onion - Stepla бесплатная помощь психолога онлайн. Часто сайт маркетплейса заблокирован в РФ или даже в СНГ, поэтому используют обходные зеркала для входа, которые есть на нашем сайте. Если вы знаете точный адрес «лукового» сайта, то с помощью этого же сервиса (или любого аналогичного) можете быстро получить к нему свободный доступ. Именно по этому мы будет говорить о торговых сайтах, которые находятся в TOR сети и не подвластны блокировкам. Многие из них не так эффективны, как хотелось. Вот и я вам krn советую после ссылки совершения удачной покупки, не забыть о том, чтобы оставить приятный отзыв, Мега не останется в долгу! Главное зеркало: mega555kf7lsmb54yd6etzginolhxxi4ytdoma2rf77ngq55fhfcnyid. Сайты вместо Гидры По своей сути Мега и Омг полностью идентичны Гидре и могут стать не плохой заменой. Всегда перепроверяйте ту ссылку, на которую вы переходите и тогда вы снизите шансы попасться мошенникам к нулю. Onion - RetroShare свеженькие сборки ретрошары внутри тора strngbxhwyuu37a3.onion - SecureDrop отправка файлов и записочек журналистам The New Yorker, ну мало ли yz7lpwfhhzcdyc5y.onion - Tor Project Onion спи. Onion - the Darkest Reaches of the Internet Ээээ. Покупателю остаются только выбрать "купить" и подтвердить покупку. Есть много полезного материала для новичков. И все же лидирует по анонимности киви кошелек, его можно оформить на левый кошелек и дроп. В сети существует два ресурса схожих по своей тематике с Гидрой, которые на данный момент заменили. Onion/ - Годнотаба открытый сервис мониторинга годноты в сети TOR. Проект создан при поддержке форума RuTor. W3C html проверка сайта Этот валидатор предназначен для проверки html и xhtml кода сайта разработчиками на соответствие стандартам World Wide Web консорциума (W3C). Onion - Konvert биткоин обменник. Сайт ramp russian anonymous marketplace находится по ссылке: ramp2idivg322d.onion. Мега Даркнет не работает что делать? "Да, и сами администраторы ramp в интервью журналистам хвастались, что "всех купили добавил. А как попасть в этот тёмный интернет знает ещё меньшее количество людей. Увидев, что не одиноки, почувствуете себя лучше. Hydra больше нет! 3дрaвcтвуйте! Поисковики Настоятельно рекомендуется тщательно проверять ссылки, которые доступны в выдаче поисковой системы. После этого отзывы на russian anonymous marketplace стали слегка пугающими, так как развелось одно кидало и вышло много не красивых статей про админа, который начал активно кидать из за своей жадности. Information премьера Adam Maniac Remix Премьера сингла! Мы не успеваем пополнять и сортировать таблицу сайта, и поэтому мы взяли каталог с одного из ресурсов и кинули их в Excel для дальнейшей сортировки. Только так получится добиться высокого уровня анономизации новых пользователей. Готовы? Silk Road (http silkroadvb5piz3r.onion) - ещё одна крупная анонимная торговая площадка (ENG). Onion - Just upload stuff прикольный файловый хостинг в TORе, автоудаление файла после его скачки кем-либо, есть возможность удалять метаданные, ограничение 300 мб на файл feo5g4kj5.onion. Onion - простенький Jabber сервер в торе. Залетайте пацаны, проверено!