Kraken зеркало стор
Ресурс был доступен через сеть Tor, по меньшей мере, с 2015. Фрезы изготовлены из высокопрочной стали и покрыты нитридом титана для увеличения срока службы. Знакомство с анонимной сетью Tor для начинающих. Piterdetka 2 дня назад Была проблемка на омг, но решили быстро, курик немного ошибся локацией, дали бонус, сижу. Для этого просто нужно добавить выбранное изделие в виртуальную корзину, заполнить форму заказа и подтвердить покупку. Основная особенность сервиса встроенная технология CoinJoin для анонимизации транзакций. Onion Archetyp Market площадка полностью посвящена ПАВ, и работает только с криптовалютой Monero. Сейчас в России существует несколько сот сайтов с зеркалами. Сейчас 305 гостей и ни одного зарегистрированного пользователя на сайте. Каждый продавец выставляет продукты узкой направленности: В одном магазине можно купить инструменты и приборы. Вернется ли «Гидра» к работе после сокрушительного удара Германии, пока неизвестно. Хотя к твоим услугам всегда всевозможные словари и онлайн-переводчики. Файлы одинаковые - выбираем любую ссылку и качаем. Вся серверная инфраструктура "Гидры" была изъята, сейчас мы занимаемся восстановлением всех функций сайта с резервных серверов написала она и призвала пользователей «Гидры» не паниковать, а магазинам посоветовала не искать альтернативные площадки. Если она будет успешной, тогда будет открыт статус "Оплачено". Изредка по отношению к некоторым вещам это желание вполне оправдано и справедливо, однако чаще всего - нет. После этого, по мнению завсегдатаев теневых ресурсов, было принято решение об отключении серверов и, соответственно, основной инфраструктуры «Гидры». Tor скроет вашу личность в Сети, скроет всё то, что вы делали в Интернете и куда ходили. И тут на помощь им приходит анонимная сеть Tor. Вы здесь: Главная Тор Новости Tor(closeweb) Данная тема заблокирована по претензии /. «Демократические реформы» в мире идут полным ходом. Можно утверждать сайт надежный и безопасный. В ведомстве считают, что более 100 млн, которые прошли через криптобиржу, были связаны с даркнет-маркетами и преступностью. Клёво2 Плохо Рейтинг.60 5 Голоса (ов) Рейтинг: 5 / 5 Пожалуйста, darknet оценитеОценка 1Оценка 2Оценка 3Оценка 4Оценка. Иногда кое-какой контроль встречается на отдельных сайтах, когда их владельцы устанавливают правила для своих посетителей. Они должны были зарегистрироваться и пополнять свой баланс, с которого средства (криптовалюта) списывалась продавцам (магазинам). Не так давно устраивался «поход» против, скажем так, нетрадиционного порно, в сети Tor. Гидра будет работать? Onion и The Abyss (http nstmo7lvh4l32epo. Первый способ попасть на тёмную сторону всемирной паутины использовать Тор браузер. Так какой же официальная ОМГ это очень удобно, потому что вам не нужно выходить из дома.
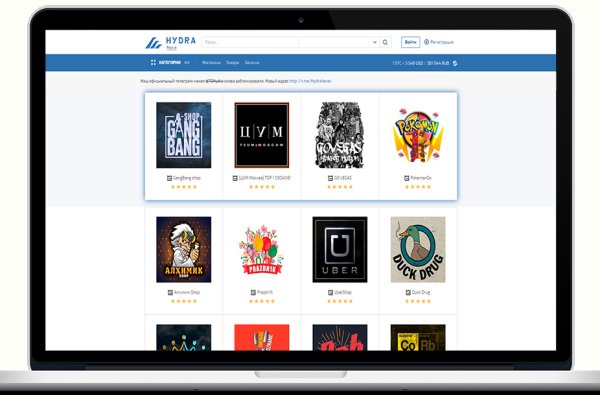
Kraken зеркало стор - Кракен гидра даркнет
Проверь свою удачу! Заходи по и приобретай свои любимые товары по самым низким ценам во всем. Низкие цены, удобный поиск, широкая география полетов по всему миру. Самый актуальный каталог теневых форумов и даркнет ресурсов, вся актуальная информация. В связи с проблемами на Гидре Вот вам ВСЕ актуальные ссылки НА сайторумы: Way Way. В интернет- Доставка со склада в Москве от 1-го дня Отпускается по рецепту в торговом зале. Array Array У нас низкая цена на в Москве. Использование VPN и Tor. Отзывы клиентов сайта OMG! Оставляет за собой право блокировать учетные записи, которые. В ближайшей аптеке, сравнить. Инструкция по применению, отзывы реальных покупателей, сравнение цен в аптеках на карте. 1 2011 открыта мега в Уфе (25 августа) и Самаре (22 декабря). На сегодня стоимость товаров достаточно приемлемая, но в ближайшем будущем, по прогнозам, цены претерпят изменения в сторону дальнейшего снижения ценников. Отрицательные и положительные стороны. Топовые товары уже знакомых вам веществ, моментальный обменник и куча других разнообразных функций ожидают клиентов площадки даркмаркетов! Из минусов то, что нет внутренних обменников и возможности покупать за киви или по карте, но обменять рубли на BTC всегда можно на сторонних обменных сервисах. Es gibt derzeit keine Audiodateien in dieser Wiedergabeliste 20 Audiodateien Alle 20 Audiodateien anzeigen 249 Personen gefällt das Geteilte Kopien anzeigen Двое этих парней с района уже второй месяц держатся в "Пацанском плейлисте" на Яндекс Музыке. В статье я не буду приводить реализацию, так как наша цель будет обойти. Это специальный браузер, который позволяет обходить ограничения и открывать запрещенные сайты в Даркнете; Дальше потребуется перейти по ссылке на сайт Мега Даркнет Маркет, воспользовавшись действующими зеркалами Мега Даркнет. Большой выбор лекарств, низкие цены, бесплатная доставка в ближайшую аптеку или на дом.по цене от 1038 руб. Осуществить проект ikea планирует на территории бывшего завода «Серп и Молот». Жанр: Спектакль для тех, кто смотрит. Truth Social совершенно новая социальная сеть, в которой можно обмениваться постами, фотографиями, новостями и прочим контентом с другими участниками. Вам необходимо зарегистрироваться для просмотра ссылок. Что такое OMG! Дождь из - обычная погода в моем округе. Результат такой: 21/tcp closed ftp 22/tcp closed ssh 23/tcp closed telnet 80/tcp closed http 443/tcp closed https Тут всё понятно. 4599 руб. Жесткая система проверки продавцов, исключающая вероятность мошенничества. Расширенный поиск каналов. Всё чаще, регулярнее обновляются шлюзы, то есть зеркала сайта. Весь каталог, адрес. ОМГ! Можно утверждать сайт надежный и безопасный. Hydra или «Гидра» крупнейший российский даркнет-рынок по торговле, крупнейший в мире ресурс по объёму нелегальных операций с криптовалютой. Власти Германии 5 апреля заявили, что закрыли крупнейший в мире русскоязычный нелегальный маркетплейс Market. 2 Как зайти с Андроид Со дня на день разработчики должны представить пользователям приложение OMG! «Мелатонин» это препарат, который поможет быстрее заснуть, выровнять циркадные ритмы. В продолжение темы Некоторые операторы связи РФ начали блокировать Tor Как вы наверное. Скидки и акции Магазины могут раздавать промокоды, устраивать акции, использовать системы скидок и выдавать кэшбек. Где теперь покупать, если Гидру закрыли? Годнотаба - список ссылок с onion зоны.
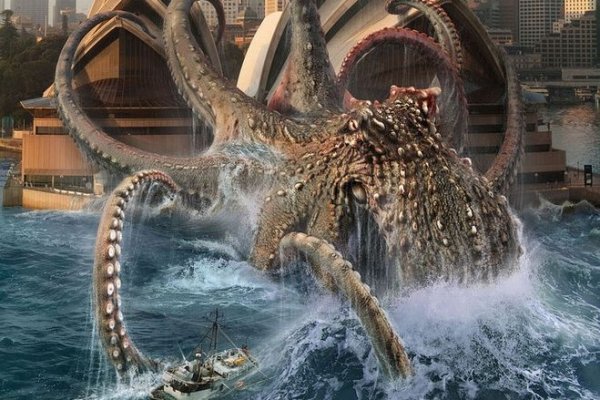
Помогаем найти нужный доступ, помогаем найти правильное зеркало на меге. Подробнее об этом рынке читайте здесь rket Royal Market это рынок даркнета, который стремится стать одним из крупнейших рынков в ближайшем будущем, ознакомьтесь с обзором этого рынка дарквеба здесь royalmarket. Поэтому убедитесь, что у вас в кошельке есть необходимая сумма для оплаты. Дать однозначный ответ на этот вопрос при всем желании не получается и вот почему: поисковых фильтров всего шесть, отсутвует некоторые фильтры которые являются очень важными и удочество. Криптовалюта должна быть внесена на рыночный кошелек, а затем может быть использована либо для оплаты покупок, либо для аренды статуса магазина и закрытых аукционов. До недавнего времени Mega Darknet Market не мог похвастаться широкой популярностью, поэтому для новичков, которые впервые знакомятся с этим рынком, мы написали пошаговые руководства о том, как что-либо делать на Mega Darknet Market, и мы ожидаем, что они будут вам полезны. Для получения доступа необходимо войти в свой аккаунт, а если его еще нет, то пройти процесс регистрации. Mega Сайт For programmers Mega onion In order to get into the main team. Снятие в касание. Именно поэтому все дарк маркеты любят именно эти зеркала или домены онион. Но все же многие по старинке предпочитают старый знакомый qiwi кошелек. Напоминалка как войти на сайт Проверка на безопасность введение капчи; Создание личного аккаунта; Регистрация (введение логина и пароля Поиск страны, города, товара, веса; Пополнение баланса криптовалютой; Осуществление сделки; Подтверждение оплаты; Получение координат товара; Поиски клада. Не могу не отметить, что внешний вид и содержание профиля магазина не соответствуют всем требованиям традиционного рынка даркнета, почему-то отсутствуют разделы: описания, политика возврата и политика соглашения. Цены на продукцию не высокие, доступные для обывателя, к тому же конкуренция пока не большая, так что продавцам не выгодно их взвинчивать. Самая безопасная криптовалюта. Для желающих закупиться в оптовым размерах действует комиссия в размере всего-лишь 1 от суммы покупки! Если вы не нашли подходящее для вас предложение в "Моментальные перейдите в раздел "Предзаказ" и попробуйте договориться с магазином например об уникальном варианте доставки, количестве и других вещах, которые вы не можете найти в уже существующих предложения. К тому же главное удобство сайта в том, что можно решит ь любой вопрос не выходя из дома и не светиться нигде. Даже политика его поставщиков впечатляет. В случае блокировки ссылки имеются приватные мосты от The Tor Project, которые помогут ее обойти. Скачайте Nord VPN и подключитесь к его серверам Onion over TOR. Все данные проходят через несколько узлов, шифруются, нельзя отследить, кто и зачем вошел в Даркнет. Рассказывают о Тор браузере, ВПН, правильных рабочих зеркалах и так далее. In the onion browser, enter the ссылка Мега онион in the search bar. Рекомендуем время от времени проверять не презентовали ли приложение. Мой рейтинг регестрации на Mega Darknet Market составляет 10 баллов из 10 возможных. Чтобы не искать ее каждый раз, сохраните ее в закладках.
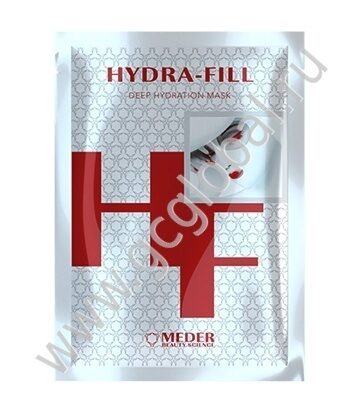
Большой выбор магазинов в твоем регионе. Омг омг сайт стал работать стабильнее. По опросам пользователей darknet в СНГ, 90 считают, что площадка omg кракен сделана идеальна с точки зрения безопасности и удобства. Была проведена огромная работа по защите данных пользователей, сохранение анонимности - приоритетная задача omg сайта. Перейди по omg ссылке и оставь отзыв о работе с ресурсом. Pinky and the Brain drug store 5300 сделок Пинки и Брейн продают самый качественный стафф! ВСУ выследили контрабанду наркотиков в РФ Правоохранительные органы Украины накрыли источник отправки запрещенных наркотических средств в Россию Схема гениальна и проста, наркотики поставляли. Omg omg площадка будет рада остановленным отзывам клиентов. 7UP сделок Магазин работает с 2017 года! Научим пользоваться купонами, скидками или наценками. Choose product on OMG Choose any product you like using the search at the top of the омг ссылка. Мы размещаем только официальные ссылки на mega на нашем сайте. Follow our link to OMG сайт and get a welcome bonus. Register on OMG Registration in two steps without mail with complete anonymity on the площадка омг. Omg omg сайт даркнет OMG OMG We hope that this site omgomg will not show itself from a bad side. Удобно. Omg omg onion - это отличное место, которое по душе каждому. Всегда с Вами! Если ты работал у нас, мы готовы продолжить двигаться с тобой в новых условиях! ОМГ and OMG сайт link's. Выбирай и покупай Теперь для тебя открыты сотни товаров в твоем городе которые ты можешь купить всего в пару кликов. На сайте вы увидите кнопку входа и регистрации. Рабочее зеркало mega mega сайт Преимущества высокий уровень безопасности; покупки с минимальными временными затратами; гарантия 100 анонимности Используется 2FA защита площадки PGP ключ для безопасности. ОМГ сайт Initially, only users of iOS devices had access to the mobile version, since in 2019, a Tor connection was required to access the omgomg. Be sure of the reliability of this omg сайт, because it was essentially left by the site administrators themselves. На Гидре было почти 500к сделок! Add balance on ОМГ Our site accepts bitcoin as payment, but will soon start accepting Monero for lightning-fast replenishment. Убедись сам и оставь обратную связь. Omgomg сайт представил самый широкий выбор товаров и услуг в даркнет. Omg omg onion площадка Omg omg onion площадка достаточно молодая. Актуальную ссылку на омг в зоне onion становится найти сложнее. The omg сайт is undergoing lightning-fast fixes and work on bugs. Осторожно переходите только по официальным зеркалам ОМГ. Пожалуйста, будьте внимательней по какой ссылке вы переходите. Войти на сайт стало гораздо проще, чем ранее заходили на hydra. OMG сайт may be able to become sales leaders in the CIS countries and gain a strong leadership in the darknet. Действительно ли это так? Регистрируйся и пополняй баланс Пройди простую регистрацию на сайте и выбери пункт полнить баланс. Среднее время регистрации на omg сайте занимает одну минуту. Testimonials сайт OMG! Недавно починили работу чата. We will be glad if you write to us and leave your feedback about omg omg сайт.