Кракен пишет пользователь не найден
Иногда случается так, что зависает именно Hydra. Ошибка в диспуте 1 Многие подписчики, которые просят помочь с диспутом часто совершают кракена одну критическуюаОшибка в диспуте 1 Многие подписчики, которые просят помочь с диспутом часто совершают одну критическую ошибку, после которой уже трудно реабилитироваться в глазах магазина/модератора. Богатый функционал Самописный движок сайта (нет уязвимостей) Система автогаранта Обработка заказа за секунды Безлимитный объем заказа в режиме предзаказа. Подробнее Диалог с Закладчиком площадка кидает кладменов не иди работать в даркнет гидра посадят кладмен. The Misunderstanding of Faith No More - Pitchfork (англ.). Я имела возможность, находясь по работе в Бишкеке, попробовать местный жидкий Метадон, потом была на конференции в Амстердаме и там я пробовала местный Метадон. Система рейтингов покупателей и продавцов (все рейтинги открыты для пользователей). Я из Одессы. Я стала в программу очень легко, без проблем. 1 декабря, в Международный день солидарности с ВИЧ-позитивными людьми, мы хотим представить вашему вниманию историю одной из нас женщины, которая живет с ВИЧ и наркозависимостью, и которая посвятила часть своей жизни поддержке других женщин, имеющих сходные проблемы. Mega - это аналог старой доброй гидры, где Вы всегда сможете легко найти и купить нужный Вам товар. Человеку, не употребляющему наркотики (в случае подброса необходимо при личном допросе при понятых указать на то, что наркотик подбросили, указать на лицо, которое его подбросило, требовать изъятия смывов с ваших рук и рук человека, подбросившего наркотик. Как загрузить фото в диспут на Hydra не могу зайти на гидру Гидра (залив фотографии, 3 способа). Созданная на платформе система рейтингов и возможность оставлять отзывы о магазинах минимизирует риски для клиента быть обманутым. Казалось бы: нет ничего проще, чем отправить снимок. Некоторые западные наркотики уже стали в России дефицитными. О ВИЧ я узнала в нашей одесской тюрьме, потому что меня закрывали в очередной раз из-за употребления наркотиков. Американские независимые лейблы SST Records, Twin/Tone Records ( рус., Touch and Go Records и Dischord Records были инициаторами смещения интереса аудитории от хардкорного панка, который в то время доминировал на андеграундной сцене, к более разнообразным стилям альтернативного рока. Tor Project позиционирует себя как анонимное пространство для свободного общения, и по их данным.5 всех пользователей Tor браузера посещают сайты даркнета. «Ну, это 2 месяца всего лишь. "Так, а что "по закону"? Редко пользователи не могут загрузить фото с мобильного устройства даже после действий, описанных выше, но с компьютера успех должен быть 100. Перейти можно по кнопке ниже: Перейти на OMG! Процесс трейда очень прост, для успешного обмена Вам необходимо: Выбрать направление обмена. Для безопасности с вашей стороны в большей степени. Впоследствии использование термина «эмо» переросло пределы музыкального жанра, став ассоциироваться с модой, стрижками и любой музыкой, выражающей эмоции 285. Ваши действия и решения должны быть направлены на максимальное сокращение сфабрикованной доказательной базы. Далее Но Подробнее КАК зайтаркнет НА андроид На случай подмены продукта или недовеса. Ни полиция, ни суд. Оригинальная ссылка на площадку Solaris http sol4rumnzchftkaieccft65drf45ky56ldqaj7tvyrgmaanh723335id. У solaris программистов всегда есть работа и они следят за тем, чтобы доступ к сайту был всегда по разным каналам. Синтаксис параметров в этом случае будет выглядеть так: адрес_страницы:имя_поля_логинаuser имя_поля_пароляpass произвольное_полезначение:строка_при_неудачном_входе Строка запуска: hydra -l user -P /john. И первое, что я сделала, это стала на учет к инфекционисту. Установите флажок "Преобразовывать загруженные файлы в формат Google". ОМГ вход В наше время, в двадцать первом веку, уже практически все люди планеты Земля освоили такую прелесть, как интернет. В первую очередь, особенно если ничего не происходит при нажатии иконки фотоаппарата в чате диспута, нужно включить java-script в TOR-браузере, из которого и зашли на Гидру. Альтернатива может представлять собой музыку, бросающую вызов статусу-кво «яростно крамольную, антикоммерческую и антимейнстримовую однако термин также используется в музыкальной индустрии, чтобы обозначить «выбор, доступный потребителям с помощью магазинов аудиозаписей, радио, кабельного телевидения и интернета». Если фото на Гидру все равно не загружается. Приносим извинения за временные неудобства». Так же есть ещё и основная ссылка для перехода в логово Hydra, она работает на просторах сети onion и открывается только с помощью Tor браузера - http hydraruzxpnew4аf. Другие способы отправки изображений на Гидре. Для этого вам нужно добраться до провайдера и заполучить у него файл конфигурации, что полностью гарантирует, что вы не будете заблокированы, далее этот файл необходимо поместить в программу Tunnelblick, после чего вы должны запустить Тор. П.). Кто стал главным претендентом на место монополиста и что он получит, если сможет победить, разобралась «Лента. Многие сайты блокируют за нарушения или просто предоставления определенных услуг. За услуги сервиса взимается как отправить фото в диспуте на гидре небольшая комиссия. Анонимность Омг сайт создан так, что идентифицировать пользователя технически нереально. Последние посты канала: Красный магазин.
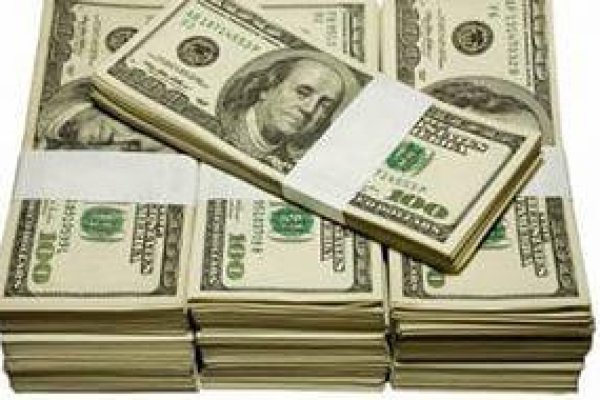
Кракен пишет пользователь не найден - Что такое кракен маркетплейс
Org, список всех.onion-ресурсов от Tor Project. Ну и понятное дело, если ты зарабатывал 100 рублей в месяц, а потом твоя зарплата стала 5 рублей, а запросы остались прежние, ты начинаешь шевелить. По слухам основной партнер и поставщик, а так же основная часть магазинов переехала на торговую биржу. Вы можете получить более подробную информацию на соответствие стандартам Вашего сайта на странице: validator. Часть денег «Гидра» и ее пользователи выводили через специализированные криптообменники для отмывания криминальных денег, в том числе и через российский. Все права защищены. На самом деле это сделать очень просто. Все первоначальные конфигурации настраиваются в автоматическом режиме). Интернету это пойдёт только на пользу. Литература Литература flibustahezeous3.onion - Флибуста, зеркало t, литературное сообщество. Часто ссылки ведут не на маркетплейс, а на мошеннические ресурсы. Кто чем вместо теперь пользуется? If you have Telegram, you can view and join Найдено в даркнете right away. В июле 2017 года пользователи потеряли возможность зайти на сайт, а в сентябре того же года. Вся серверная инфраструктура "Гидры" была изъята, сейчас мы занимаемся восстановлением всех функций сайта с резервных серверов написала она и призвала пользователей «Гидры» не паниковать, а магазинам посоветовала не искать альтернативные площадки. Годнотаба - список ссылок с onion зоны. Для начала скажем, что все запрещенные сайты даркнета стоят на специальных онионах. Этот сайт упоминается в сервисе социальных закладок Delicious 0 раз. Зеркало сайта z pekarmarkfovqvlm. Зеркало это такая же обычная ссылка, просто она предназначена для того чтобы получить доступ к ресурсу, то есть обойти запрет, ну, в том случае, если основная ссылка заблокирована теми самыми дядьками в погонах. Оригинальный сайт: ore (через TOR browser) / (через Тор) / (онион браузер).Сборник настоящих, рабочих ссылок на сайт мега в Даркнете, чтобы вы через правильное, рабочее зеркало попали на официальный сайт Меги. Если быть точнее это зеркала. В итоге купил что хотел, я доволен. Он несколько замедляет работу браузера, обещая при этом «бесплатное полное шифрование трафика а для его активации требуется ввести адрес электронной почты. Еще один способ оплаты при помощи баланса смартфона. Сам же сайт включает в себя множество функций которые помогают купить или продать вес буквально автоматизированно, и без лишних третьих лиц. Оригинальное название mega, ошибочно называют: mego, мего, меджа, union. Не попадайтесь на их ссылки и всегда будете в безопасности. PGP, или при помощи мессенджера Jabber. Telefon oder E-Mail Passwort Забирай! Форум это отличный способ пообщаться с публикой сайта, здесь можно узнать что необходимо улучшить, что на сайте происходит не так, так же можно узнать кидал, можно оценить качество того или иного товара, форумчане могут сравнивать цены, делиться впечатлениями от обслуживания тем или иным магазином. Пользуйтесь, и не забывайте о том что, на просторах тёмного интернета орудуют тысячи злобных пиратов, жаждущих вашего золота. Mega Darknet Market не приходит биткоин решение: Банально подождать. Многие и многое шлют в Россию. Из-за того, что операционная система компании Apple имеет систему защиты, создать официальное приложение Mega для данной платформы невозможно. Данный сервер управляется панелью управления BrainyCP. Onion - Tor Metrics статистика всего TORа, посещение по странам, траффик, количество onion-сервисов wrhsa3z4n24yw7e2.onion - Tor Warehouse Как утверждают авторы - магазин купленного на доходы от кардинга и просто краденое. Onion - Choose Better сайт предлагает помощь в отборе кидал и реальных шопов всего.08 ВТС, залил данную сумму получил три ссылки. Именно на форуме каждый участник имеет непосредственную возможность поучаствовать в формировании самого большого темного рынка СНГ Hydra. Onion - Cockmail Электронная почта, xmpp и VPS.
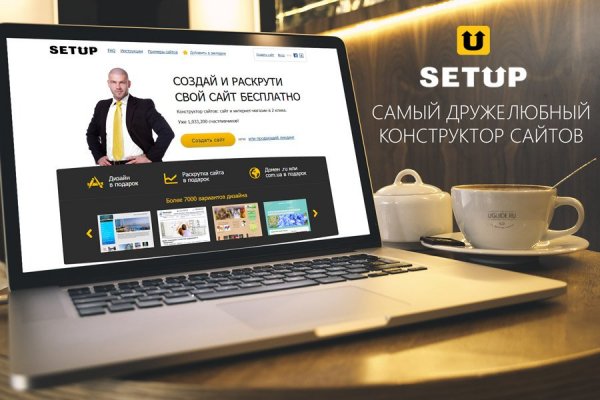
Onion - Cockmail Электронная почта, xmpp и VPS. Основные усилия направлены на пресечение каналов поставок наркотиков и ликвидацию организованных групп и преступных сообществ, занимающихся их сбытом». Она защищает сайт Mega от DDoS-атак, которые систематически осуществляются. Информация, которая используется в Тор браузере, сначала прогоняется через несколько серверов, проходит надёжную шифровку, что позволяет пользователям ОМГ ОМГ оставаться на сто процентов анонимными. Onion - Схоронил! . Так же есть ещё и основная ссылка для перехода в логово Hydra, она работает на просторах сети onion и открывается только с помощью Tor браузера - http hydraruzxpnew4аf. Похоже? Требуется регистрация, форум простенький, ненагруженный и более-менее удобный. Во-вторых, плагин часто превращает вёрстку заблокированных страниц в месиво и сам по себе выглядит неопрятно. По словам Артёма Путинцева, ситуация с Hydra двойственная. Такой глобальный сайт как ОМГ не имеет аналогов в мире. Vabu56j2ep2rwv3b.onion - Russian cypherpunks community Русское общество шифропанков в сети TOR. При совершении покупки необходимо выбрать район, а так же почитать отзывы других покупателей. Как только соединение произошло. А если уж решил играть в азартные игры с государством, то вопрос твоей поимки - лишь вопрос времени. Matanga уверенно занял свою нишу и не скоро покинет насиженное место. Языке, покрывает множество стран и представлен широкий спектр товаров (в основном вещества). Мы выступаем за свободу слова. Rospravjmnxyxlu3.onion - РосПравосудие российская судебная практика, самая обширная БД, 100 млн. Расследование против «Гидры» длилось с августа 2021. Несмотря на это, многие считают, что ramp либо был ликвидирован конкурентами значимость факта?, либо закрыт новыми администраторами значимость факта? Legal обзор судебной практики, решения судов, в том числе по России, Украине, США. Почему именно mega darknet market? Зеркало сайта. Всё, что надо знать новичку. Приложения для смартфонов Самым очевидным и самым простым решением для пользователей iPhone и iPad оказался браузер Onion, работающий через систему «луковой маршрутизации» Tor (The Onion Router трафик в которой почти невозможно отследить. Как зайти 2021. Что-то про аниме-картинки пок-пок-пок. При этом на полной скорости машина может разгоняться до 350 километров в час. Например, с помощью «турбо-режима» в браузере Opera без проблем удалось открыть заблокированный средствами ЖЖ блог Алексея Навального, однако зайти на сайт, доступ к которому был ограничен провайдером, не вышло. Сервис от Rutor. Данный сервер управляется панелью управления BrainyCP. Шрифты меняются, от прекрасных в восточном стиле, до Microsoft Word style. Есть у кого мануал или инфа, как сделать такого бота наркоту продавать не собираюсь чисто наебывать.
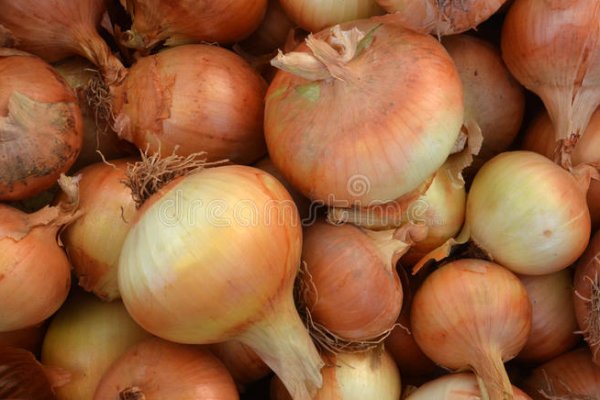
WELCOME TO THE HERO FACTORY.Prodotti aspirazionali, manager ispirazionali:
il mercato ha bisogno di eroi.
Ed eroi si diventa. Spesso, insieme a noi.
Da 30 anni il successo di manager, brand e prodotti
passa per BPRESS.Be the next hero.HOW TO MAKE A HERO.Come nasce un hero product?Come si presenta un prodotto e si racconta un brand per attirare l’attenzione dei potenziali clienti? Come si differenzia dalla concorrenza? Il nostro incarico comincia proprio qui, creando la strategia di comunicazione più adatta e lavorando duramente per fare diventare brand e prodotti i protagonisti di uno stile di vita. E noi partiamo da quello che ti aspetti da un’agenzia di PR: le relazioni con i giornalisti e i blogger per creare interesse e visibilità sui media tradizionali e online, il dialogo con gli influencer наркотиками e i brand ambassador attraverso i social media, la progettazione di eventi e la produzione di contenuti multimediali. Uniamo media relations e comunicazione tradizionale con i nuovi linguaggi del video making e dello storytelling. Cioè, per usare una parola di moda: ci occupiamo di content marketing.Come far parlare di un’azienda?Aiutando i manager a dialogare con la business community. Studiando competitor e mercati, parlando quotidianamente con i giornalisti-chiave e con i blogger,organizzando incontri, interviste ed eventi con i media nazionali, locali e verticali cartacei, on air e on line. Insomma, facendo tutto quello che è utile per favorire il dialogo con gli influencer sui temi-chiave. Risultato: i manager delle aziende per cui lavoriamo crescono in autorevolezza e riconoscibilità. Perché la comunicazione corporate oggi passa attraverso il personal branding del top management, il media training e le speaking opportunities. Ma anche attraverso contenuti di qualità, interessanti per i media e per le community dei clienti. E poi, sperando di doverlo fare il meno possibile, affianchiamo l’azienda nel crisis management.Be the next hero.I nostri eroiSCOPRILI TUTTIDicono di noiNFONGrande conoscenza del mercato e degli opinion leader, contatti chiave nel mondo dei media e abilità nel trasmettere e amplificare i messaggi strategici, nei tempi e nei modi corretti: in BPRESS non abbiamo trovato solo l’eccellenza in questi ambiti ma anche un team capace di anticipare le nostre richieste, di proporre idee e contenuti di qualità e di un dinamismo contagioso. Marco Pasculli, VP International Revenue Operations – NFONBABBELBabbel si è posizionata nel tempo come punto di riferimento e realtà esperta nel campo dell’educazione, oltre che come fonte autorevole di dati e informazioni per differenti tipologie di media. Non solo in ambito strettamente linguistico, ma in un contesto più ampio associato al mondo della cultura, della tecnologia, della carriera e del lifestyle. Per raggiungere questo traguardo il team BPRESS è stato fondamentale, grazie a un lavoro costante di content creation, che ci ha permesso di trasmettere i vantaggi del metodo Babbel, di raggiungere le differenti tipologie dei nostri utenti e di ottenere una media coverage sempre in crescita e di grande qualità.Raquel Meca Garrido, Senior International PR Manager Spain, Italy, France – BABBELLINEA MAMMABABYLa brand essence rappresenta il cuore e l’anima di un’azienda e il Team BPRESS è riuscito da subito, con velocità e grande competenza, a cogliere l’essenza del nostro marchio. E questo è fondamentale per un brand come Linea MammaBaby, pensato per un target allargato, i bambini e l’intera famiglia. Abbiamo lanciato insieme nuovi prodotti, con successo, e siamo riusciti finalmente a fare quel cambio di passo nella comunicazione, sia sui mezzi tradizionali, sia sui canali social!Maria Elena Olcelli, CEO – LINEA MAMMABABYNEXTDOORIn BPRESS ho trovato innanzitutto un partner, non solo un consulente. Ho trovato un alleato, che mi ha affiancato negli anni, nella comunicazione strategica e operativa. Ho trovato un team sempre disponibile e appassionato che, fin dal lancio di Nextdoor in Italia, non ha mai smesso di creare campagne Pr particolarmente smart, tanto da essere più volte fonte di ispirazione per le agenzie di comunicazione delle altre country europee in cui siamo presenti.Amedeo Galano, Head of Italy – NEXTDOORDoppietta di premi per BPRESS ai Touchpoint Awards Engagement 2021R3START! TV, la web tv in live streaming sui canali FB e di BPRESS, si aggiudica il primo premio di categoria Comunicazione Corporate Il lancio di Le Mani sul Mondo, primo podcast Audible Original di Roberto Saviano in esclusiva per Audible.it – nell’ambito di Maratona Podcast – Tramedautore –...