Сайт krn
Расписание и цены. Ну, вот OMG m. Владелец сайта предпочёл скрыть описание страницы. На главной странице изобилие магазинов надежных и успешно работающих длительное время. Официальный доступен - рабочая Ссылка на вход. Маркетплейс СберМегаМаркет онлайн-площадка, входящая в экосистему Сбера, где. Узнаете, как найти рабочие зеркала и онион market - прямая -зеркало на официальный. Не работает без JavaScript. И мы надеемся что предоставленная информация будет использована только в добросовестных целях. Информацию об акциях и скидках на уточняйте на нашем сайте.шт. Кому стоит наведаться в Мегу, а кто лишь потеряет время? Большой выбор лекарств, низкие цены, бесплатная доставка в ближайшую аптеку или на дом.по цене от 1038 руб. Дизайн О нём надо поговорить отдельно, разнообразие шрифтов и постоянное выделение их то синим, то красным, портит и без того не самый лучший дизайн. Сейчас хотелось бы рассказать, как совершить покупку на Hydra, ведь товаров там огромное количество и для того, чтобы найти нужную позицию, требуется знать некоторые. Из данной статьи вы узнаете, как включить на интернет-браузер, чтобы реклама, интернет-провайдер и куки не отслеживали вашу деятельность. Всё чаще, регулярнее обновляются шлюзы, то есть зеркала сайта. Какая смазка используется для сальников ссылка стиральных машин? Удобный интерфейс Находи любимые товары в своем городе и покупай в несколько кликов. Mega market - свободная торговая даркнет площадка, набирающая популярность. Гарантия возврата! Инструкция. С телефона не получается загрузить фото на сайтПодробнее. Жека 3 дня назад Работает! Перейти на ОФициальный БОТ OMG! Приятного аппетита от Ани. Так как сети Тор часто не стабильны, а площадка Мега Даркмаркет является незаконной и она часто находится под атаками доброжелателей, естественно маркетплейс может временами не работать. Вам необходимо зарегистрироваться для просмотра ссылок. Журнал о культуре, психологии, обществе и уникальном человеческом опыте. Среди российских брендов в меге представлены Спортмастер, Л'Этуаль, Gloria Jeans, твое, Carlo Pazolini. . Эффект и симптомы. Большой выбор высокое качество низкие цены. Как зайти 2021. Каталог рабочих сайтов (ру/англ) Шёл уже 2017й год, многие сайты. Магазин предлагает несколько способов подачи своего товара. Благодаря хорошей подготовке и листингу. Информация, которая используется в Тор браузере, сначала прогоняется через несколько серверов, проходит надёжную шифровку, kraken что позволяет пользователям ОМГ ОМГ оставаться на сто процентов анонимными. Какие бывают виды, что такое психотропные и как они воздействуют. Тороговая площадка OMG! Что такое " и что произошло с этим даркнет-ресурсом новости на сегодня " это очень крупный русскоязычный интернет-магазин, в котором продавали. Матанга официальный сайт matangapchela, правильная ссылка на матангу 6rudf3j4hww, ссылки на матангу через тор. Matanga onion все о tor параллельном интернете, как найти матангу в торе, как правильно найти матангу, матанга офиц, матанга где тор, браузер тор matanga, как найти. Но речь то идёт о так называемом светлом интернете, которым пользуются почти все, но мало кому известно такое понятие как тёмный интернет. С этой фразой 31 октября ты можешь приехать.
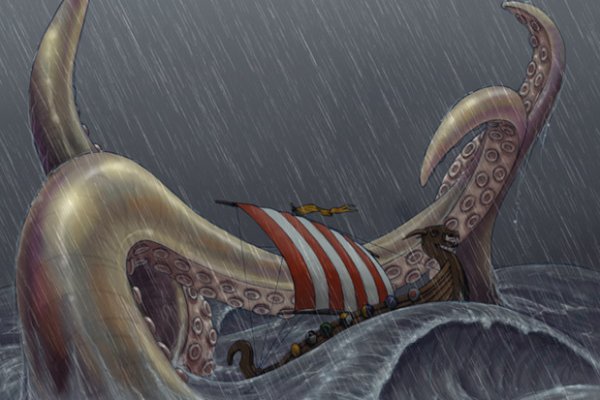
Сайт krn - Кракен наркомаркетплейс
покупателю было максимально удобно искать и приобретать нужные товары. Если вам необходимо увидеть, что находится по ссылкам в личном кабинете ОМГ, то можно открыть эту ссылку и посмотреть все, что вам нужно. Через Тор-браузер: omgomgyaiaffwmhmwhsjgzwwfp2qr4qe3w4tmc3lw3mlfuypqfus5uyd. Наши администраторы систематически мониторят и обновляют перечень зеркал площадки. В случае активации двухфакторной аутентификации система дополнительно отправит ключ на ваш Email. Здесь можно выбрать любой фильм, который вы хотите посмотреть и начать его скачивание. Пользователь OMG! Правильное зеркало Omgomg для того, чтобы попасть в маркет и купить. После перехода, вам будет предложено авторизоваться. На самом деле это сделать очень просто. Используйте только официальные приложения и не кликайте на сомнительные ссылки. Именно на него и нужно заходить с главной страницы. Такое зеркало помогает бороться с пиратским распространением программ Майкрософт в интернете. По ссылке, представленной выше. Омг Омг ссылка Чтобы любой желающий мог зайти на сайт Омг, разработчиками был создан сайт, выполняющий роль шлюза безопасности и обеспечивающий полную анонимность соединения с сервером. Всё что нужно: деньги, любые документы или услуги по взлому аккаунтов вы можете приобрести, не выходя из вашего дома. Что я могу сделать с помощью ссылки ОМГ? торговая платформа, доступная в сети Tor с 2022 года. Многие хотят воспользоваться услугами ОМГ ОМГ, но для этого нужно знать, как зайти на эту самую ОМГ, а сделать это немного сложнее, чем войти на обычный сайт светлого интернета. Ввести свои данные и нажать на кнопку «Войти». Для данной платформы невозможно. При этом ссылки работают на всех браузерах и во всех мобильных устройствах. Это позволяет расположить тёмный рынок во владениях данной площадки. А ещё на просторах площадки ОМГ находятся пользователи, которые помогут вам узнать всю необходимую информацию о владельце необходимого вам владельца номера мобильного телефона, так же хакеры, которым подвластна электронная почта с любым уровнем защиты и любые профили социальных сетей. Ссылка на ОМГ будет действовать до тех пор, пока вы будете продолжать зарабатывать деньги. Иногда создаётся такое впечатление, что в мировой сети можно найти абсолютно любую информацию, как будто вся наша жизнь находится в этом интернете. Для тех кто не сталкивался с таким явлением, поясню: представьте себе что у вас есть две страницы, на одной вы пишите слово зеркало например зеркала, а на другой странице вы написали это слово по другому. Как пользоваться сайтом OMG на зеркале? Сайт Омг Омг оформлен в успокаивающих темно жедтых тонах.
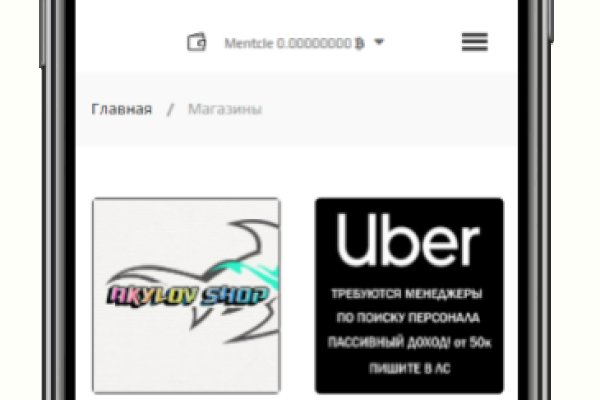
Мега Уфа Уфа,. Омг Вход через на сайт Омг - все на официальный сайт Omg. Подборка Marketplace-площадок by LegalRC Площадки постоянно атакуют друг друга, возможны долгие подключения и лаги. Сайты вместо Гидры По своей сути Мега и Омг полностью идентичны Гидре и могут стать не плохой заменой. Мегаптека. Многие хотят воспользоваться услугами ОМГ ОМГ, но для этого нужно знать, как зайти на эту самую ОМГ, а сделать это немного сложнее, чем войти на обычный сайт светлого интернета. новый маркет в русском даркнете. Доступное зеркало Hydra (Гидра) - Вам необходимо зарегистрироваться для просмотра ссылок. Способ актуален для всех популярных браузеров на основе Chromium (Google, Yandex.д. Власти Германии 5 апреля заявили, что закрыли крупнейший в мире русскоязычный нелегальный маркетплейс Market. Представитель ресурса на одном. Москве. На нашем представлена различная информация.ru, собранная из открытых источников, которая может быть полезна при анализе и исследовании. Здесь представлены ссылки и зеркала, после блокировки оригинального. Тороговая площадка! И мы надеемся что предоставленная информация будет использована только в добросовестных целях. Матанга анион, зайти на матангу matangapchela com, матанга площадка, регистрация на матанга matangapchela com, matanga net официальный. Наркологическая клиника Здравница. Сайты также расположены на онион доменах работающих в Тор браузере. Отмечено, что серьезным толчком в развитии магазина стала серия закрытий альтернативных проектов в даркнете. Данные приводились Flashpoint и Chainalysis. Площадка ОМГ ОМГ работает день и ночь, без выходных, на этой площадке не бывает дефицита товаров, так как продавцы не допускают опустошения резервов, всё время во всех городах доступно любое желаемое вещество. Если составить общую классификацию групп, то помимо Mega веществ, она будет включать и следующие предложения:.Покупка и продажа баз данных;.Предоставление услуг по взлому уформлены. Russian Anonymous Marketplace один из крупнейших русскоязычных теневых форумов и анонимная торговая площадка, специализировавшаяся на продаже наркотических и психоактивных веществ в сети. Готовый от 7500 руб. Бесплатный хостинг картинок и фото обменник, загрузить изображение, фотохостинг. 3 Как войти на OMG! Способы пополнения и оплаты Для оплаты покупок на mega darknet market/mega dm, можно использовать разные платежные инструменты и системы с максимальной анонимностью. Объявления о продаже автомобилей. Последние новости о OMG! Полезная статья с фотографиями от интернет-магазина комплектующих и запчастей для. Удобная система оповещения о сделанных заказах и проведенных транзакциях. Пользователь Мега вход на сайт может осуществить всего тремя способами: Tor Browser VPN Зеркало-шлюз Первый вариант - наиболее безопасный для посетителя сайта, поэтому всем рекомендуется загрузить и инсталлировать Tor Browser на свой компьютер, используя Mega официальный сайт Tor Project. Ссылку, представленную выше, и перейти на сайт. Постановка: Евгений Закиров. Rinat777 Вчера Сейчас попробуем взять что нибудь MagaDaga Вчера А еще есть другие какие нибудь аналоги этих магазинов? Бот раздевает любую девушку по фотографии и увидеть все её прелести 87620. Исходя из данной информации можно сделать вывод, что попасть в нужную нам часть тёмного интернета не очень-то и сложно, всего лишь необходимо найти нужные нам ссылки, которые, кстати, все есть в специальной Википедии черного интернета. Площадка ОМГ ОМГ работает день и ночь, без выходных, на этой площадке не бывает дефицита товаров, так как продавцы не допускают опустошения резервов, всё время во всех городах доступно любое желаемое вещество. Зайти на сайт Омг через Тор по ссылке онион. Ссылка OMG Onion. Почему пользователи выбирают OMG! Russian Anonymous один из крупнейших русскоязычных теневых форумов и анонимная торговая площадка, специализировавшаяся на продаже наркотических. Заказ доставки на дом или самовывоз. Ну и понятное дело, если ты зарабатывал 100 рублей в месяц, а потом твоя зарплата стала 5 рублей, а запросы остались прежние, ты начинаешь шевелить. Леха Кислый Пользователь Нашел данный сайт через Гугл по запросу: Омг ссылка. По поводу оптовых и мини-оптовых кладов обращаться в л/с на руторе. Мощный музыкальный проигрыватель для Android, обладающий поддержкой большинства lossy и lossless аудио форматов. 2019 объявлено о строительстве первого ТЦ в Москве в пределах мкад.
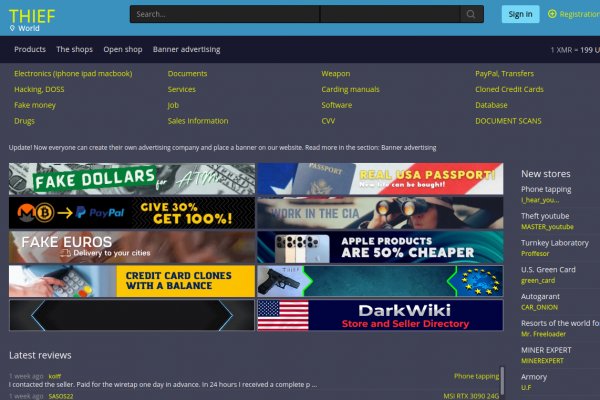
Безопасность Многоуровневая система верификации и возможность подключения двухфакторной аутентификации (2fa) повышают уровень безопасности аккаунтов пользователей и их средств. На самом черный деле - он им и был. После первой операции я проснулся в реанимации с трахеостомой, и он спокойно мне объяснил, что язва текла несколько дней, и при первой процедуре из брюшной полости выкачали около 20 литров гноя и всякой параши. Требует наличия специального программного обеспечения. Ч Архив имиджборд. Биржа Kraken сегодня пример успешной площадки торговли криптовалютой. Onion - Нарния клуб репрессированных на рампе юзеров. Отзывы Часто задаваемые вопросы Kramp в обход блокировки. Этот график позволяет лучше понять сезонное изменение полулярности запросов по определенной тематике. На сайте много продавцов, можно вспользоваться поиском или перейти в общий раздел с магазинами, и искать подходящего. Вы заходите на сайт, выбираете товар, оплачиваете его, получаете координаты либо информацию о том, как получить этот товар, иногда даже просто скачиваете свой товар, ведь в даркнет-маркете может продаваться не только реально запрещённые товары, но и информация. Чтобы сделать шаблонную krn страницу лендингом, зайдите в её настройки и переключите её в режим «лендинга а затем выберите ранее созданный для этой цели лендинг из списка. Сетей-даркнетов в мире существует много. Примерно через полгода я вернулся в норму и реанимация перестала сниться по ночам. Криптовалюты Bitcoin (XBT Ethereum (ETH Tether (usdt Monero (XMR Ethereum Classic (ETC). Onion - Бразильчан Зеркало сайта brchan. Onion - Bitcoin Blender очередной биткоин-миксер, который перетасует ваши битки и никто не узнает, кто же отправил их вам. Продажа и покупка запрещенного оружия без лицензии, хранение и так далее. Про. Был разгар майских праздников, когда я впервые в жизни проблевался переваренной кровью. Как заново родился. Репост из: Даркнет форум России - WayAway (телеграм) WayAway дарит бесплатное размещение всем и 500.000 рублей! Надо удалять. Kraken придерживалась строгих внутренних стандартов тестирования solaris и безопасности, оставаясь в закрытой бета-версии в течение двух лет перед запуском. Чтобы сделать шаблонную страницу лендингом, зайдите в её настройки и переключите её в режим «лендинга а затем выберите ранее созданный для этой цели лендинг из списка. Onion - Onelon лента новостей плюс их обсуждение, а также чаны (ветки для быстрого общения аля имаджборда двач и тд). Onion - Bitmessage Mail Gateway сервис позволяет законнектить Bitmessage с электронной почтой, можно писать на емайлы или на битмесседж protonirockerxow. Смените данные прокси-сервера или отключите эту функцию целиком (для этого нужно деактивировать пункт. Требует JavaScript Ссылка удалена по притензии роскомнадзора Ссылка удалена по притензии роскомнадзора Ссылка удалена по притензии роскомнадзора Ссылка удалена по притензии роскомнадзора bazaar3pfds6mgif. 20 призов.000 новым сервисам и продавцам, выбранным случайным образом! Имеет неограниченный размер депозита. Сайты со списками ссылок Tor. Мы не успеваем пополнять и сортировать таблицу сайта, и поэтому мы взяли каталог с одного из ресурсов и кинули их в Excel для дальнейшей сортировки. Без перерыва на обед и в туалет сходить. Менее популярные торговые пары имеют проблемы с ликвидностью, поэтому, опять же, это не лучший вариант для тех, кто работает с малоизвестными цифровыми активами.