Как восстановить аккаунт кракен
Портал автопродаж закладок в кракен инетрнете мега сайт даркнет ссылка Кто в наше время не пользуется инетом? Здесь Вы найдете все ссылки на ресурсы мега, как в onion зоне, так и в telegram. Покупатель ищет закладку по координатам и фото. Но существует иной интернет, мало кому известный, его зовут темный. Также велик риск нарваться на мошенников. Перейти айфона mega onion магазины мега мега даркнет маркет это не отдельный магазин. Продажа стаффа в сети TOR. Неплохой вариант в плане безопасности это XMR. Конкурентоспособные цены мега сайт для беспрецедентной ценности Мега даркнет площадка гордится своей глобальной доступностью. Абсолютно всем мы помогаем войти на mega. Двухфакторка устанавливается через PGP-ключ. То есть вашу реальную личности невозможно привязать с деятельностью на Меге. Перечень товаров просто огромен, ассортимент постоянно пополняется. Д. Далее происходит проверка и пользователь видит необходимый адрес. Если Вы хотите работать в нашей команде, то будем рады рассмотреть Ваше резюме. Следите за тем, как часто обновляются зеркала, внимательно пересматривайте ссылки на предмет мошенничества и старайтесь заходить только по официальным ссылкам. Данный сайт занимается распространением запрещенной продукции и находится в доменной зоне onion, поэтому войти в него можно только с использованием TOR браузера. Получаем у провайдера файл конфигурации, это поможет уйти от блокировки. Пытаясь конкурировать с Гидрой, продавцы снижают цены, что очень радует потребителей. Это сделано для обеспечения вашей безопасности. А оплата в криптовалюте также анонимна, невозможно отследить кто платил и откуда. На мега даркнет сайт мы не идем на компромиссы в отношении качества. Процесс контроля качества на Mega даркнет сайт включает строгие проверки, которые каждый товар должен пройти, прежде чем стать доступным на нашем мега зеркало. Поддержка Mega зеркало для бесперебойной торговли. Ссылка mega storаркнете много аферистов и мошенников, поэтому легко попасться на их удочку и остаться без денег, а иногда и аккаунта. Под понятие тип товара подразумевают форму его маскировки. Mega Darknet Market ссылка Какие функции имеются на сайте Мега Успешно авторизовавшись, пользуйтесь всеми функциями сайта без ограничений: Каталог с адресами и ассортиментом магазинов. Мы стремимся обеспечить доступность и удобство нашей платформы для всех. Категорически запрещается торговать: Фентанилом и его производными, поскольку он может привести к смерти человека и очень пагубно действует на организм; Любыми кладами и службами в странах Европы и Америки, за это могут вовсе сайт закрыть. Вопрос: Сайт часто недоступен. Mega Darknet Market - даркнет маркетплейс мега по продаже товаров в теневом интернете. Ссылка на сайт мега для входа через VPN и ТОР. Mega Darknet Market - это маркетплейс по продаже Ваших любимых товаров в теневом интернете. Ссылка на сайт мега для входа через ТОР. Jun 10, 2023 Mega Тор доступ к маркетплейсу через даркнет программу. Вход на Мегу, маркетплейс для покупки маркетплейс наркотиков, осуществляется через Тор-браузер, который предоставляет доступ к даркнету. Эта. Jul 9, 2023 mega market - даркнет площадка через Tor Browser! Как зайти на сайт. Мега маркет онион в Тор? Ссылка -зеркало на darknet shop mega onion. Mega onion ссылка на даркнет магазин в тор Mega 4af рабочие зеркала на моментальные магазины в даркнете Площадка с наркотиками повсюду, в телеграме, в tor, в center web. Анонимный мир мега даркнет, где вы можете найти огромный выбор продуктов и насладиться защитой эскроу.
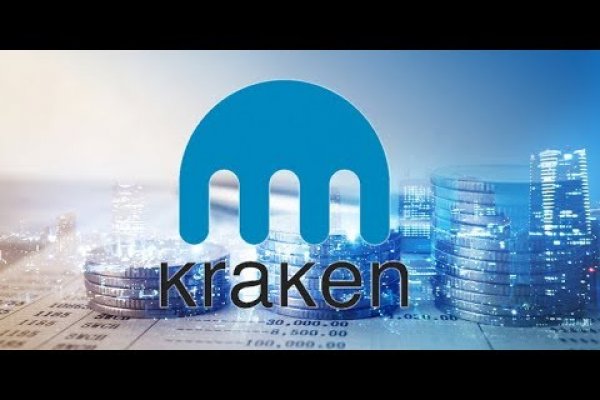
Как восстановить аккаунт кракен - Kraken пользователь не найден при входе
Onion - Архив Хидденчана архив сайта hiddenchan. Всем привет, в этой статье я расскажу вам о проекте ТОП уровня defi, у которого. Ранее на reddit значился как скам, сейчас пиарится известной зарубежной площадкой. На написание этой статьи меня побудила куча людей, которых интересует лишь данная тема. Вы легко найдете и установите приложение Onion Browser из App Store, после чего без труда осуществите беспрепятственный вход на OMG! Источник p?titleМега сеть_торговых_центров) oldid. Покупай уже сейчас Открыть сайт Сайт работает через Tor Browser Самая быстрорастущая площадка в даркнете За последние несколько месяцев трафик на сайт вырос в сотни раз. Федяково,. Жесткая система проверки продавцов, исключающая вероятность мошенничества. Что за? Данные отзывы относятся к самому ресурсу, а не к отдельным магазинам. Уводят аккаунт при обмене. Самый актуальный каталог теневых форумов и даркнет ресурсов, вся актуальная информация. Танки Онлайн первый многопользовательский браузерный 3D-боевик. Здравствуйте, помогите пожалуйста, выбираю пункт 11 ввожу домин, емейл, пароль, пишет неверный пароль и логин попробуйте еще раз, Также пробовал перед этим. Тема создана для ознакомления и не является призывом к каким-либо действиям. На счёт последней причины вам будет отказано в разбане! Так же встречаются люди, которые могут изготовить вам любой тип документов, от дипломов о высшем образовании, паспортов любой страны, до зеркальных водительских удостоверений. Форум hydra кидалы m заказал клад на 300 через гаранта,. Объявления о продаже автомобилей. «Мелатонин» это препарат, который поможет быстрее заснуть, выровнять циркадные ритмы. Оставите жалобу на если вас обманули на гидре. Только сегодня узнала что их закрылся. Залетайте пацаны, проверено! Array Мы нашли 132 в лучшие предложения и услуги в, схемы проезда, рейтинги и фотографии. Мега, Белая Дача: адреса со входами на карте, отзывы, фото, номера телефонов, время. 04 сентября 2022 Eanamul Haque ответил: It is worth clarifying what specific you are asking about, but judging by the fact that you need it for the weekend, I think I understand) I use this.
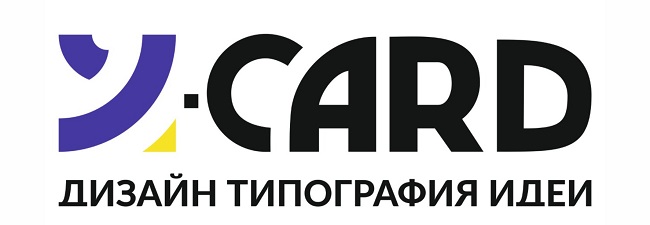
У меня для вас очень плохие новости. Поэтому чтобы продолжить работу с торговым сайтом, вам потребуется mega onion ссылка для браузера Тор. Мега Нижний Новгород Нижегородская область, Кстовский район,. Мега официальный магазин в сети Тор. Как правильно загрузить фото в?Подробнее. Перейти можно по кнопке ниже: Перейти на OMG! Привет, танкисты! Расширенный поиск каналов. Hydra русскоязычная торговая площадка в сети, признанная крупнейшим маркетплейсом даркнета. Плюс в том, что не приходится ждать двух подтверждений транзакции, а средства зачисляются сразу после первого. Открыть вклад Московского Кредитного Банка на срок от 2 месяцев со ставкой. Единственное "но" хотелось бы больше способов оплаты. Наркологическая клиника Здравница. Дождь из - обычная погода в моем округе. В наших аптеках в Москве капсулы. Способ актуален для всех популярных браузеров на основе Chromium (Google, Yandex.д. Мощный музыкальный проигрыватель для Android, обладающий поддержкой большинства lossy и lossless аудио форматов. Для этого отсканируйте. Обновлено Вам необходимо удалить лимит для загрузки без ограничений? Все зеркала onion. Пользователь empty empty задал вопрос в категории Прочее образование и получил на него. Бот для Поиска @Mus164_bot corporation Внимание, канал несёт исключительно музыкальный характер и как место размещения рекламы! Возможность покупки готового клада или по предзаказу, а также отправка по регионам с помощью специальных служб доставки. Это займет пару минут. В ТОР. Правильная! Почему пользователи выбирают OMG! Вход на портал. Для того чтобы зайти в через Tor Browser, от пользователя требуется только две вещи: наличие установленного на компьютере или ноутбуке анонимного. Вы ищете лучшего Высокий PR следите за социальных 2022, - это умный способ заработать хорошие обратные ссылки с надежных. Russian Marketplace один из крупнейших русскоязычных теневых форумов и торговая площадка. 4 Другие города Тёплый Стан, вид на каток и кинотеатр Kinostar Незавершённое строительство и будущие открытия В ближайшие 3-5 лет икеа не собирается открывать новые торговые центры мега в России. Что за m? Леха Кислый Пользователь Нашел данный сайт через Гугл по запросу: Омг ссылка. Санкт-Петербурге и по всей России Стоимость от 7500. Если вы получили аккаунта, то эта статья вам поможет. Пользователь OMG! FK-: скейт парки и площадки для катания на роликах, самокатах, BMX. Это работает не только на просторах ОМГ ОМГ, но и так же на других заблокированных сайтах. Мега, Белая Дача: адреса со входами на карте, отзывы, фото, номера телефонов, время. Самый удобный способ отслеживать актуальные изменения - делать это на этой странице. 7/10 (52 голосов) - Search бесплатно. С телефона не получается загрузить фото на сайтПодробнее. Большой выбор высокое качество низкие цены. Ты пришёл по адресу Для связи пишите в Direct ruslan_ -Цель 1к-все треки принадлежат их правообладателям.
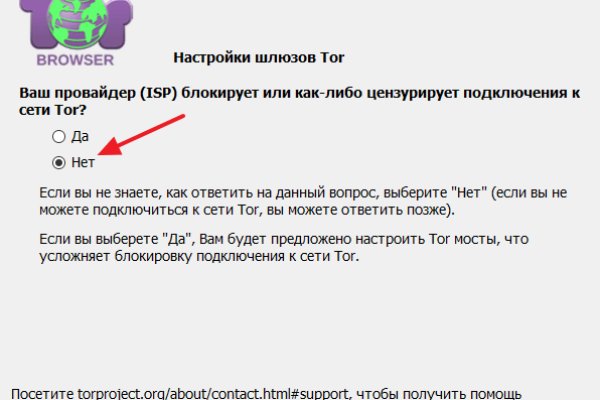
Правила сайта net omgFycazuС 1 января номинал карты кракен увеличен с трёх до пяти тысяч рублей. 1санкт-петербург, Невский проспект 114-116, литера ахабаровск, Пионерская 2вapple BOX москва, Чонгарский бульвар, 7саратов, Зарубина, 167нижний новгород, Большая Покровская, 82apple BOX москва, Лескова, 14казань, Павлюхина, 91волгоград, Рабоче-Крестьянская, кракен 9бпермь,. В 2022 году к «Пушкинской карте»…